Device for improving sheet rushing during pouring
A technology of punching and gate, applied in the direction of coating, etc., can solve the problems of inability to plastic injection on the sheet, difficult to reach the lamination area, and overturning of the sheet, so as to avoid leakage of raw materials and cooperate closely with each other. , the effect of increasing the tightness
- Summary
- Abstract
- Description
- Claims
- Application Information
AI Technical Summary
Problems solved by technology
Method used
Image
Examples
Embodiment Construction
[0011] The preferred embodiments of the present invention will be described below in conjunction with the accompanying drawings. It should be understood that the preferred embodiments described here are only used to illustrate and explain the present invention, and are not intended to limit the present invention.
[0012] A device for improving the feeding and punching sheet, such as figure 1 Shown, comprise first mold 17 and second mold 18, the inboard of first mold 17 offers first pouring groove 20, the inner side middle part of first pouring groove 20 installs single-point hot nozzle 22, the inboard of first mold 17 is installed into The gate 23, the gate 23 is located at the side of the first pouring trough 20, the inner side of the second mold 18 is provided with a second pouring trough 21, the second pouring trough 21 can be fastened with the first pouring trough 20, the first mold 17 A locking and fastening device is installed between the second mold 18, and the locking...
PUM
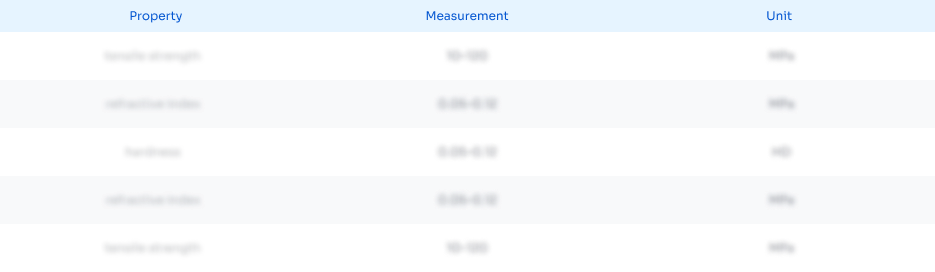
Abstract
Description
Claims
Application Information

- R&D Engineer
- R&D Manager
- IP Professional
- Industry Leading Data Capabilities
- Powerful AI technology
- Patent DNA Extraction
Browse by: Latest US Patents, China's latest patents, Technical Efficacy Thesaurus, Application Domain, Technology Topic, Popular Technical Reports.
© 2024 PatSnap. All rights reserved.Legal|Privacy policy|Modern Slavery Act Transparency Statement|Sitemap|About US| Contact US: help@patsnap.com