Co-precipitation reactor
A reaction kettle and co-precipitation technology, applied in chemical/physical/physical chemical fixed reactors, chemical/physical/physical chemical processes, chemical instruments and methods, etc., can solve the problem of large relative supersaturation and poor dispersion effect up and down , affect product quality and other issues, to achieve the effect of low relative supersaturation, sufficient and rapid mixing, and improve product quality
- Summary
- Abstract
- Description
- Claims
- Application Information
AI Technical Summary
Problems solved by technology
Method used
Image
Examples
Embodiment Construction
[0017] The present invention will be further described below in conjunction with accompanying drawing and specific embodiment:
[0018] The present invention as figure 1 Or as shown in 2 or 3, a co-precipitation reaction kettle includes a kettle body 1, a stirring device 2 with a stirring blade 4 and a feeding device 3 are installed on the kettle body 1, wherein the feeding device 3 includes a feeding pipe 5, It is characterized in that: the bottom end of the feed pipe 5 is located at the bottom of the kettle body. In this embodiment, a feed port 6 is opened on the side wall of the feed pipe 5 . In this embodiment, the length of the feed pipe 5 is 1.8 meters. In this embodiment, there are 4-7 feed ports 6 . In this embodiment, there are six feed ports 6 . In this embodiment, the feed opening 6 increases sequentially from the upper part to the lower part. In this embodiment, the distance between each of the feed ports 6 is 50mm.
[0019] The feed pipe extends to the botto...
PUM
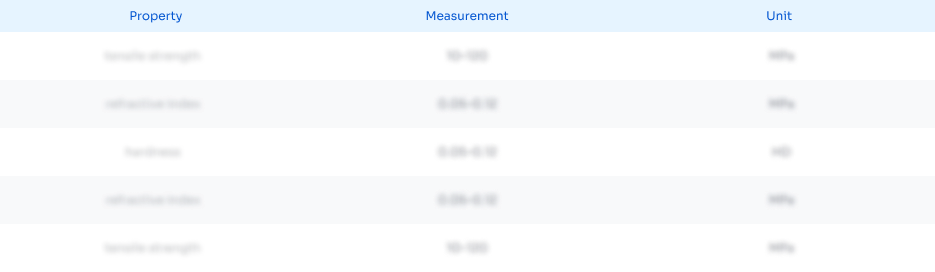
Abstract
Description
Claims
Application Information

- R&D
- Intellectual Property
- Life Sciences
- Materials
- Tech Scout
- Unparalleled Data Quality
- Higher Quality Content
- 60% Fewer Hallucinations
Browse by: Latest US Patents, China's latest patents, Technical Efficacy Thesaurus, Application Domain, Technology Topic, Popular Technical Reports.
© 2025 PatSnap. All rights reserved.Legal|Privacy policy|Modern Slavery Act Transparency Statement|Sitemap|About US| Contact US: help@patsnap.com