Self-lubricating contact device for low-temperature liquid pump and using method of self-lubricating contact device
A low-temperature liquid and contact device technology, which is applied to components of pumping devices for elastic fluids, liquid fuel engines, pump components, etc., can solve problems such as liquid medium vaporization seals, failure, and temperature rise of liquid contact surfaces, and achieve Improve the dynamic pressure effect, reduce frictional heat, and achieve the effect of no leakage
- Summary
- Abstract
- Description
- Claims
- Application Information
AI Technical Summary
Problems solved by technology
Method used
Image
Examples
Embodiment 1
[0021] Embodiment 1, with reference to attached Figure 1-4 , to further describe the present invention:
[0022] A self-lubricating contact device for a cryogenic liquid pump mentioned in the present invention includes a gland 1, a spring 2, a push plate 3, a stationary ring 6, a rotating ring 8, and a shaft sleeve 13. A groove is provided on one side of the gland 1, The spring 2 and the push plate 3 are connected to the stationary ring 6, and the push plate 3 enables the stationary ring 6 to have axial compensation capability. The right side of the stationary ring 6 is in contact with the rotating ring 8, and the rotating ring 8 is in contact with the The end face of the stationary ring 6 is provided with an annular groove body 7, and a plurality of drainage channels 9 are arranged inside the annular groove body 7, and concave high-pressure dynamic pressure channels are respectively provided on both sides of the annular groove body 7. The groove 16 and the low-pressure dyna...
Embodiment 2
[0028] Embodiment 2 differs from Embodiment 1 in that the number of low-pressure dynamic pressure grooves is 24; the number of the above-mentioned drainage channels 9 is 24; in addition, refer to the attached Figure 5 , the high-pressure dynamic pressure groove 16 and the low-pressure dynamic pressure groove 17 both adopt a spiral structure, specifically referring to the attached Figure 5 , under the action of viscous shear force, the liquid medium leaked from the drainage channel to the low-pressure side of the seal is returned to the sealed cavity. Function, to achieve no leakage of the sealed liquid medium.
Embodiment 3
[0029] Embodiment 3 differs from Embodiment 1 in that the number of low-pressure dynamic pressure grooves is 16; the number of the above-mentioned drainage channels 9 is 20; in addition, refer to the attached Figure 5 , the high-pressure dynamic pressure groove 16 adopts a spiral structure, the low-pressure dynamic pressure groove 17 adopts a V-shaped structure, and the middle is a ring-shaped groove body. For details, refer to the attached Figure 6 , under the action of viscous shear force, the liquid medium leaked from the drainage channel to the low-pressure side of the seal will be returned to the sealed cavity. The structure makes it disturb the flow and reverse the flow, and can also better eliminate the leakage under the action of the pressure difference, and realize no leakage of the sealed liquid medium.
PUM
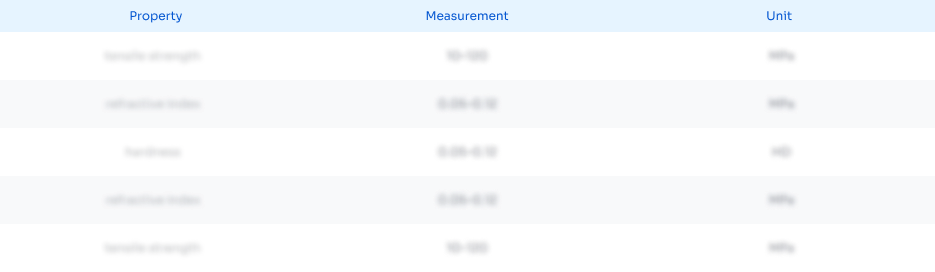
Abstract
Description
Claims
Application Information

- R&D
- Intellectual Property
- Life Sciences
- Materials
- Tech Scout
- Unparalleled Data Quality
- Higher Quality Content
- 60% Fewer Hallucinations
Browse by: Latest US Patents, China's latest patents, Technical Efficacy Thesaurus, Application Domain, Technology Topic, Popular Technical Reports.
© 2025 PatSnap. All rights reserved.Legal|Privacy policy|Modern Slavery Act Transparency Statement|Sitemap|About US| Contact US: help@patsnap.com