A method for exploiting coalbed methane by using burning coal seam to assist fracture making
A technology for coalbed methane and coalbed methane wells, which is applied in the fields of fluid production, earthwork drilling, wellbore/well components, etc., can solve problems such as sand plugging, fracturing fluid filtration, and difficulty in construction, and avoid compaction. effect, improve the effect of reconstruction, no effect of fracturing fluid pollution
- Summary
- Abstract
- Description
- Claims
- Application Information
AI Technical Summary
Problems solved by technology
Method used
Image
Examples
Embodiment 1
[0052] Example 1. Coalbed methane reservoir fire reformation
[0053] 1) For selected coalbed methane wells, the depth is 1128.4-1136.8m, the thickness is 5.6m, and the gas content is 15.31-19.36m 3 / t, the gas saturation is 71-89%, the initial test gas hardly produces gas, first inject nitrogen (N 2 ) (can also inject carbon dioxide (CO 2 )) The gas pushes the coalbed methane near the wellbore to about 5m deep in the formation (equivalent to 25000m under ground conditions 3 ), to achieve the purpose of isolation between air injection and coalbed methane in the later stage, and to avoid the risk of explosion caused by direct contact between air injection and coalbed methane.
[0054] 2) Lower the electric heating igniter into the bottom of the well, inject air to ignite, the ignition temperature is guaranteed to be above 500°C, the highest temperature is 525°C, and the initial injection speed is about 5000m 3 / d, the ignition time is 4 days, continue to inject air after tur...
Embodiment 2
[0059] Example 2. Combination reconstruction of fracturing + coalbed methane reservoir fire
[0060] 1) For selected coalbed methane wells, the depth is 606.6-609.6m, the thickness is 3m, and the gas content is 16-20m 3 / t, with a gas saturation of 73%-93%, first use high-energy gas fracturing to generate multiple fractures.
[0061] 2) Lower the electric heating igniter into the bottom of the well, inject air to ignite, the ignition temperature is guaranteed to be above 500°C, the highest temperature is 543°C, and the initial injection speed is about 8000m 3 / d, the ignition time is 5 days, turn off the igniter, continue to inject air, in order to produce more micro cracks, increase the ventilation rate to 20000m in the later stage 3 / d inject air, accumulatively inject air 40×10 4 m 3 , ignite the coal seam near the wellbore, and finally form the completion effect of caves near the wellbore, remove the pollution near the wellbore, and improve the seepage capacity of the n...
Embodiment 3
[0066] Example 3: Coalbed methane reservoir horizontal well + fire reconstruction
[0067] 1) For the selected CBM horizontal well, the length of the horizontal well section is 500m 3 , the depth of coalbed methane reservoir is 514.2-520.6m, the thickness is 5.4m, and the gas content is 16-26m 3 / t, gas saturation 90-98.9%, first inject a certain amount of nitrogen (N 2 ) gas pushes the coalbed methane near the wellbore to about 5m deep in the formation (equivalent to 60000m under ground conditions 3 ), to achieve the purpose of isolation between air injection and coalbed methane in the later stage, and to avoid the risk of explosion caused by direct contact between air injection and coalbed methane.
[0068] 2) Lower the electric heating igniter into the bottom of the well, inject air to ignite, the ignition time is 40 days, the ignition temperature is guaranteed to be above 500°C, the highest temperature is 532°C, and the initial injection speed is about 12000m 3 / d, the ...
PUM
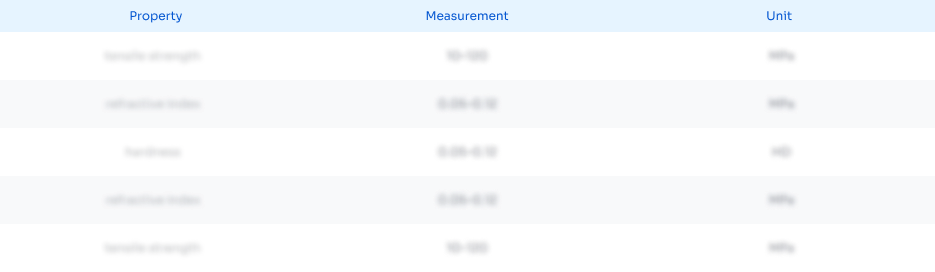
Abstract
Description
Claims
Application Information

- R&D Engineer
- R&D Manager
- IP Professional
- Industry Leading Data Capabilities
- Powerful AI technology
- Patent DNA Extraction
Browse by: Latest US Patents, China's latest patents, Technical Efficacy Thesaurus, Application Domain, Technology Topic, Popular Technical Reports.
© 2024 PatSnap. All rights reserved.Legal|Privacy policy|Modern Slavery Act Transparency Statement|Sitemap|About US| Contact US: help@patsnap.com