A Production Process of Alloy Zinc Powder for Reducing Zinc Content in Water Quenching Slag
A technology of alloy zinc powder and production process, which is applied in the field of production process of alloy zinc powder to reduce the zinc content of water quenching slag, which can solve the problems of high zinc content in slag and waste of metal zinc resources, etc., and achieve small smoke volume and fast reaction speed , The effect of short process flow
- Summary
- Abstract
- Description
- Claims
- Application Information
AI Technical Summary
Problems solved by technology
Method used
Image
Examples
Embodiment 1
[0019] A production process of alloyed zinc powder for reducing zinc content in water-quenching slag, comprising the steps of:
[0020] Step 1. Material ratio adjustment
[0021] During the batching process, the temperature of the material is heated to 180-220 ° C, and the moisture in the material is dried to below 1%. The coke excess coefficient C in the batching process is adjusted to the segmented ratio of different production periods. The coke excess coefficient in the material ratio of the normal production process is 8 -10%, the coke excess coefficient in the material ratio before shutdown and start-up is increased to 15%-18%, and the coke excess coefficient in the material ratio before slagging is increased to 20%-22%.
[0022] At present, most of the materials produced by alloy zinc powder are composed of zinc calcine, coke, quicklime, and quartz mixed according to specific process requirements. After mixing, they are added to the electric rotary kiln, and the air ente...
PUM
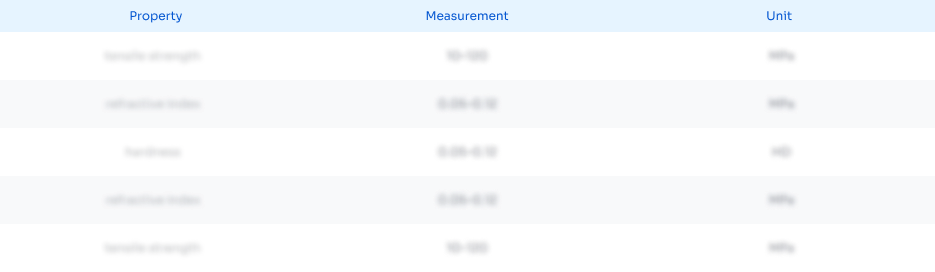
Abstract
Description
Claims
Application Information

- R&D Engineer
- R&D Manager
- IP Professional
- Industry Leading Data Capabilities
- Powerful AI technology
- Patent DNA Extraction
Browse by: Latest US Patents, China's latest patents, Technical Efficacy Thesaurus, Application Domain, Technology Topic, Popular Technical Reports.
© 2024 PatSnap. All rights reserved.Legal|Privacy policy|Modern Slavery Act Transparency Statement|Sitemap|About US| Contact US: help@patsnap.com