Flying system for unmanned aerial vehicle
A technology of unmanned aerial vehicles and flying devices, which is applied in the field of unmanned aerial vehicles to achieve the effects of fast flight speed, long battery life, and convenient take-off and landing
- Summary
- Abstract
- Description
- Claims
- Application Information
AI Technical Summary
Problems solved by technology
Method used
Image
Examples
Embodiment 1
[0026] A drone flight system such as Figure 1-2 As shown, it includes: a fixed-wing flying device and a rotary-wing flying device with variable rotation direction, and a control system that is respectively connected to the fixed-wing flying device and the rotating-wing flying device. The extension shaft 1, the tilting assembly 2 rotatably connected to at least one end of the extension shaft 1, and the electric rotor mechanism 4 connected to the outer end of the tilting assembly 2, the electric rotor mechanism 4 is connected to the tilting assembly 2 Driven by the drone, it forms a set angle with the horizontal plane to match the take-off, landing and flight of the drone. The rotation of the tilting assembly 2 drives the electric rotor mechanism 4 to change between the two directions of the horizontal plane and the vertical plane. When the electric rotor mechanism 4 rotates in the horizontal plane, the rapid take-off and landing of the UAV is realized; when the When the elect...
Embodiment 2
[0032] The difference from Embodiment 1 is that there is one extension shaft 1, the extension shaft 1 is arranged on the central axis of the fuselage, and the extension shaft 1 is parallel to or perpendicular to the central axis of the fuselage.
[0033] Only one end of the extension shaft 1 may be connected to the tilting assembly 2, or both ends of the extension shaft 1 may be connected to the tilting assembly 2. When only one end of the extension shaft 1 is connected to the tilting assembly 2, The tilting assembly 2 can be parallel to the horizontal plane when the UAV takes off and lands, so as to drive the electric rotor mechanism 4 to be parallel to the horizontal plane; it is also possible to turn the tilting assembly 2 clockwise downward on the extension shaft 1 when the UAV is flying horizontally Rotate downward or upward above the extension shaft 1 to drive the electric rotor mechanism 4 to rotate in the vertical plane to provide horizontal thrust for the horizontal di...
Embodiment 3
[0037] The difference from Embodiment 1 and Embodiment 2 is that the length of the tilting assembly 2 can be adjusted to meet the requirements of the rotating space between the tilting assembly 2 and the electric rotor mechanism 4, and the height difference between the electric rotor mechanism 4 set up.
[0038] Or the wing length of the electric rotor mechanism 4 can be adjusted to meet the requirement of the rotation space of the tilting assembly 2 and the electric rotor mechanism 4 .
[0039] During specific implementation, the number of the extension shaft 1 includes but is not limited to one in embodiment 1, and two in embodiment 2, or three or even more. The setting and installation of the extension shaft 1 The location can also be the fuselage 5 and / or the wing 3, and the working mode of the tilting assembly 2 and the electric rotor mechanism 4 can refer to embodiment 1 and embodiment 2 or combine embodiment 1 and embodiment 2.
[0040] To sum up, the flight system that ...
PUM
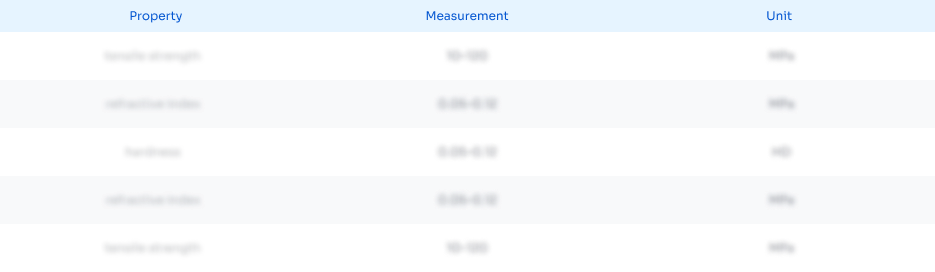
Abstract
Description
Claims
Application Information

- R&D Engineer
- R&D Manager
- IP Professional
- Industry Leading Data Capabilities
- Powerful AI technology
- Patent DNA Extraction
Browse by: Latest US Patents, China's latest patents, Technical Efficacy Thesaurus, Application Domain, Technology Topic, Popular Technical Reports.
© 2024 PatSnap. All rights reserved.Legal|Privacy policy|Modern Slavery Act Transparency Statement|Sitemap|About US| Contact US: help@patsnap.com