A wire forming machine
A forming machine and transfer forming machine technology, applied in the direction of wire material processing, spring manufacturing from wire, tool manufacturing, etc., can solve the problems of large diameter of transfer wire and the inability to achieve high-precision molding with 6 mm transfer wire, so as to reduce labor costs, The effect of high intelligence and obvious economic benefits
- Summary
- Abstract
- Description
- Claims
- Application Information
AI Technical Summary
Problems solved by technology
Method used
Image
Examples
Embodiment Construction
[0027] The present invention will be described in further detail below in conjunction with the accompanying drawings.
[0028] Figure 1 to Figure 8 A wire forming machine according to the invention is schematically shown.
[0029] For a wire forming machine provided in this embodiment, please refer to Figure 1 to Figure 8 , including: a control device 001 and an automatic discharge rack 002 electrically connected to the control device 001, a main molding machine 003 and a transfer molding machine 004;
[0030] The automatic unwinding rack 002 includes an unwinding rack 005, on which a wire turntable 006 and a wire guide are arranged, on the wire guide a broken wire detector 007 is arranged, and the wire turntable 006 The turntable drive motor 008 is connected to the bottom of the wire guide, the wire guide includes a wire bracket 009 connected to the discharge frame 005 through bolts, the wire bracket 009 is provided with a wire wheel 010, and the wire breakage detector 00...
PUM
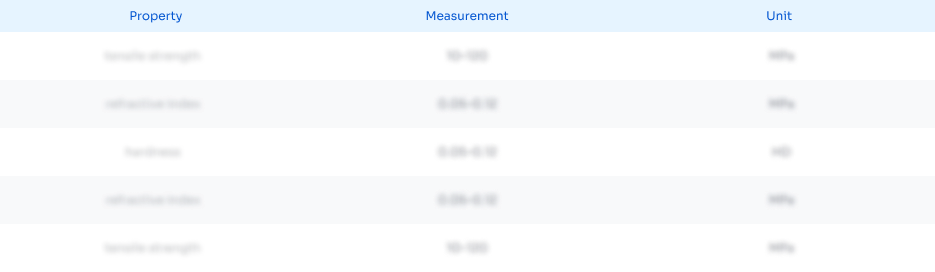
Abstract
Description
Claims
Application Information

- R&D Engineer
- R&D Manager
- IP Professional
- Industry Leading Data Capabilities
- Powerful AI technology
- Patent DNA Extraction
Browse by: Latest US Patents, China's latest patents, Technical Efficacy Thesaurus, Application Domain, Technology Topic, Popular Technical Reports.
© 2024 PatSnap. All rights reserved.Legal|Privacy policy|Modern Slavery Act Transparency Statement|Sitemap|About US| Contact US: help@patsnap.com