Method of Coal Slurry Mixed Burning in Large Proportion in Circulating Fluidized Bed Boiler
A circulating fluidized bed and large-scale technology, which is applied in the field of boiler mixed coal slime, can solve the problems of scouring and wear on the heating surface, increase in circulating ash, and high power consumption of boiler auxiliary equipment, so as to reduce the wear of the heating surface and reduce the once The effect of wind rate and boiler efficiency improvement
- Summary
- Abstract
- Description
- Claims
- Application Information
AI Technical Summary
Problems solved by technology
Method used
Image
Examples
Embodiment 1
[0043] Embodiment 1: the method for coal slime mixed with a large proportion of circulating fluidized bed boiler, which comprises the following steps: (1) coal slime screening; (2) coarse coal slime loading and unloading; (3) coarse coal slime drying in the air; ( 4) Coarse slime with qualified humidity is transported to the coal transportation system; (5) Coal transportation by the coal transportation system; (6) Coal feeding to the circulating fluidized bed boiler; (7) Combustion of coal in the circulating fluidized bed boiler; Among them,
[0044] (1) Coal slime screening: Coarse coal slime and fine coal slime are operated separately in the coal washing plant. Fine coal slime is used as the raw material of the coal slime conveying system, and the coarse coal slime is discharged through the slime belt; Moisture, viscosity and other properties are very different. When mixed into the fuel system for blending, it will easily lead to equipment blockage, reduce system output, and ...
Embodiment 2
[0063] Example 2: During the test using the method of Example 1 of the present invention, no slag cooler blockage event occurred, the boiler slag discharge was in good condition, and the carbon content of the ash remained basically stable and slightly decreased before and after the test; the boiler material cycle Normal, the load response capability remains unchanged, and all parameters are normal.
[0064] 1. Through the implementation of low bed pressure operation optimization, adjust the slag discharge system to remove a certain amount of bed material, reduce the operating bed pressure from 7KPa to about 5KPa, and maintain a stable and economical operation at a lower bed pressure. As the bed pressure decreases, the amount of circulating materials in the furnace decreases, the ability of circulating ash to take away heat decreases, the bed temperature increases, the carbon content of fly ash and bottom slag decreases, and the boiler efficiency increases; when maintaining a st...
PUM
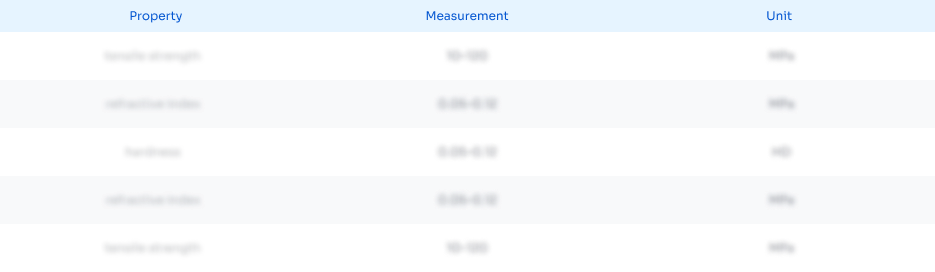
Abstract
Description
Claims
Application Information

- Generate Ideas
- Intellectual Property
- Life Sciences
- Materials
- Tech Scout
- Unparalleled Data Quality
- Higher Quality Content
- 60% Fewer Hallucinations
Browse by: Latest US Patents, China's latest patents, Technical Efficacy Thesaurus, Application Domain, Technology Topic, Popular Technical Reports.
© 2025 PatSnap. All rights reserved.Legal|Privacy policy|Modern Slavery Act Transparency Statement|Sitemap|About US| Contact US: help@patsnap.com