Active radial system for rail train
A rail train and active technology, applied in the field of rail train radial system, can solve the problems of limited reduction of wheel-rail lateral force, limited radial effect, wheel-rail wear, etc., achieve complete safety guidance function, and improve curve passing performance. , The effect of reducing wear and noise
- Summary
- Abstract
- Description
- Claims
- Application Information
AI Technical Summary
Problems solved by technology
Method used
Image
Examples
Embodiment
[0033] Such as figure 1 As shown, an active radial system of a rail train, the system is connected to a train network 1, and the system includes a train-level controller 2, a line information measurement unit 3, a vehicle-controlled volumetric servo controller 4 and an action execution unit 5, the rail train Each car body 13 is provided with a vehicle-controlled volumetric servo controller 4 and four action execution units 5 respectively connected to the vehicle-controlled volumetric servo controller 4, and the four action execution units 5 are symmetrically arranged on the vehicle body respectively. On both sides of the front bogie and the rear bogie of body 13, the line information measurement unit 3 is arranged on the head car body, and the line information measurement unit 3 and the vehicle-controlled volumetric servo controller 4 in each car body 13 are connected to the train Level controller 2, the train level controller 2 is connected to the train network 1, the train l...
PUM
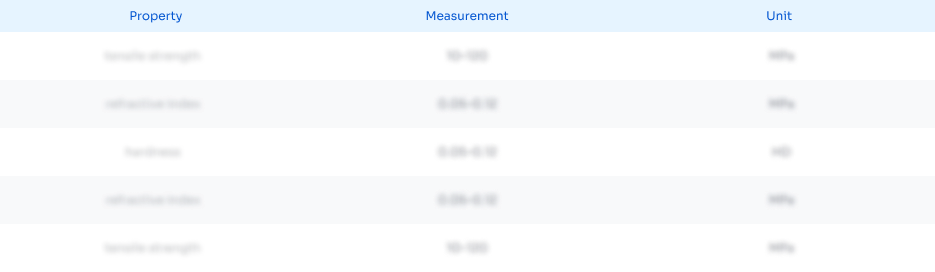
Abstract
Description
Claims
Application Information

- R&D Engineer
- R&D Manager
- IP Professional
- Industry Leading Data Capabilities
- Powerful AI technology
- Patent DNA Extraction
Browse by: Latest US Patents, China's latest patents, Technical Efficacy Thesaurus, Application Domain, Technology Topic, Popular Technical Reports.
© 2024 PatSnap. All rights reserved.Legal|Privacy policy|Modern Slavery Act Transparency Statement|Sitemap|About US| Contact US: help@patsnap.com