Fabric printing and washing process
A fabric and printing technology, which is applied in the field of fabric printing and washing process of fabrics, can solve the problems of poor layering, rough graphics, and not bright enough colors, etc., and achieve the effect of strong layering, bright colors, and not easy to fade
- Summary
- Abstract
- Description
- Claims
- Application Information
AI Technical Summary
Problems solved by technology
Method used
Examples
Embodiment 1
[0023] Embodiment one: comprise the following steps:
[0024] S1: Select the fabric and perform dust removal on the fabric;
[0025] S2: One printing treatment, printing the pretreated fabric;
[0026] S3: One wash with water, add soda ash to adjust the pH value to 10, add 1 part of CD anti-stick agent, and wash with water at 30°C;
[0027] S4: Put the semi-finished fabric into a dryer to dry at a drying temperature of 120°C;
[0028] S5: Secondary printing treatment;
[0029] S6: Second washing, adding acetic acid to the water tank to adjust the pH value to 4, adding 5 parts of KNR color fixing agent, and washing with water at 50°C to increase the color fixing rate;
[0030] S7: Wash with water and dry.
[0031] Between steps S6 and S7, steaming is also included. The high temperature and normal pressure method is 150° C., and the steaming time is 3 minutes, so as to increase the color fixing rate.
[0032] In step S5, a color fixing agent is sprayed on the surface of the...
Embodiment 2
[0033] Embodiment two: comprise the following steps:
[0034] S1: Select the fabric and perform dust removal on the fabric;
[0035] S2: One printing treatment, printing the pretreated fabric;
[0036] S3: One wash with water, add soda ash to adjust the pH value to 10.5, add 2 parts of CD anti-stain agent, and wash with water at 35°C;
[0037] S4: Put the semi-finished fabric in a dryer to dry at 125°C;
[0038] S5: Secondary printing treatment;
[0039] S6: Second washing, adding acetic acid to the water tank to adjust the pH value to 4, adding 6 parts of KNR color fixing agent, and washing with water at 55°C to increase the color fixing rate;
[0040] S7: Wash with water and dry.
[0041] Between steps S6 and S7, steaming is also included. The high temperature and normal pressure method is 160° C., and the steaming time is 5 minutes, so as to increase the color fixing rate.
[0042] In step S5, a color fixing agent is sprayed on the surface of the pattern to make the pa...
Embodiment 3
[0043] Embodiment three: comprise the following steps:
[0044] S1: Select the fabric and perform dust removal on the fabric;
[0045] S2: One printing treatment, printing the pretreated fabric;
[0046] S3: One wash with water, add soda ash to the water tank to adjust the pH value to 11, add 3 parts of CD anti-stick agent, and wash with water at 45°C;
[0047] S4: Put the semi-finished fabric into a dryer for drying at 130°C;
[0048] S5: Secondary printing treatment;
[0049] S6: Second washing, adding acetic acid to the water tank to adjust the pH value to 4.5, adding 7 parts of KNR color fixing agent, and washing with water at 60°C to increase the color fixing rate;
[0050] S7: Wash with water and dry.
[0051] Between steps S6 and S7, steaming is also included. The high temperature and normal pressure method is 175° C., and the steaming time is 6 minutes, so as to improve the color fixing rate.
[0052] In step S5, a color fixing agent is sprayed on the surface of t...
PUM
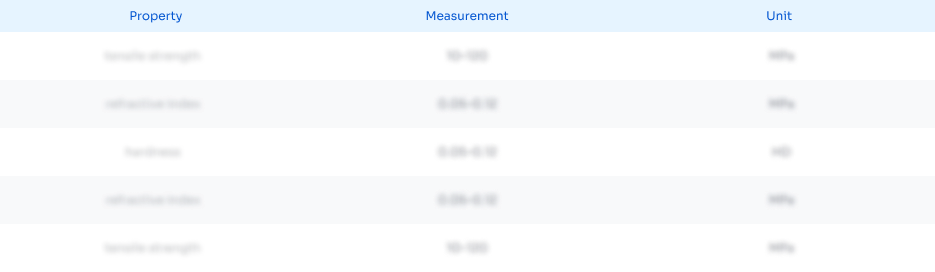
Abstract
Description
Claims
Application Information

- Generate Ideas
- Intellectual Property
- Life Sciences
- Materials
- Tech Scout
- Unparalleled Data Quality
- Higher Quality Content
- 60% Fewer Hallucinations
Browse by: Latest US Patents, China's latest patents, Technical Efficacy Thesaurus, Application Domain, Technology Topic, Popular Technical Reports.
© 2025 PatSnap. All rights reserved.Legal|Privacy policy|Modern Slavery Act Transparency Statement|Sitemap|About US| Contact US: help@patsnap.com