A transmission unit detector imaging and electrical parameter testing system
A technology of unit detectors and electrical parameters, applied in the directions of measuring electricity, measuring electrical variables, and testing optical properties, etc., can solve problems such as verification and inability to scan imaging performance at the same time, achieve low cost, strong application and market value, and realize instrumental effect
- Summary
- Abstract
- Description
- Claims
- Application Information
AI Technical Summary
Problems solved by technology
Method used
Image
Examples
Embodiment 1
[0020] An imaging operation method of a transmission type unit detector, comprising:
[0021] Step 1: The three-dimensional scanning platform automatically controls the focusing operation, completes the focusing operation of the detector in the direction of the Z axis, uses the motor control to complete the adjustment of the stage and the rotating platform, and the stage rotates to the state where the light source is fully open. When the value collected by the AD sampling module is the maximum, it is confirmed that the system focus is completed;
[0022] Step 2: Place the target object on the stage, the stage motor rotates the target object to the optical path, and the three-dimensional scanning platform uses the X-axis and Y-axis to complete the imaging and scanning of the two-dimensional plane;
[0023] Step 3: Carry out formal imaging to display the acquisition process. The data transmission flow is as follows: the detector converts the optical signal on the focal plane int...
Embodiment 2
[0026] An operation method for testing electrical parameters of a transmissive unit detector, comprising:
[0027] Step 1: The 3D scanning platform automatically controls the focusing operation, and uses the motor control to complete the adjustment of the stage and the rotating platform, so that the optical fiber light source interface is aligned with the collimator. When the value collected by the AD sampling module is the largest, it is confirmed as The system focus is completed;
[0028] Step 2: The operation interface is in the state of electrical parameter testing. After the system completes the automatic focusing, the formal parameter testing process is carried out. By adjusting the wavelength, power, pulse width and other parameters of the fiber optic light source, it enters the collimator and finally the detector The light source is an optical signal with known parameters.
[0029] The flow direction of data transmission is: the detector converts the optical signal on...
PUM
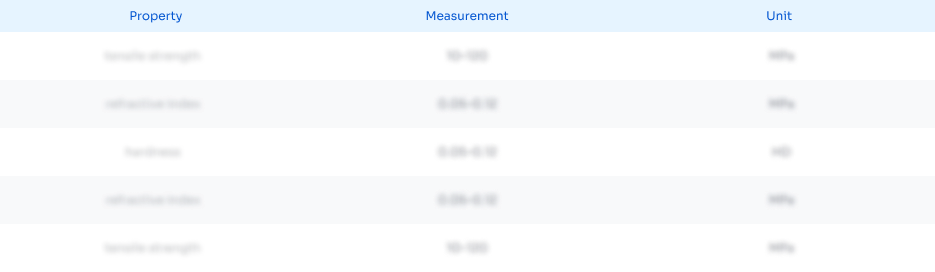
Abstract
Description
Claims
Application Information

- R&D
- Intellectual Property
- Life Sciences
- Materials
- Tech Scout
- Unparalleled Data Quality
- Higher Quality Content
- 60% Fewer Hallucinations
Browse by: Latest US Patents, China's latest patents, Technical Efficacy Thesaurus, Application Domain, Technology Topic, Popular Technical Reports.
© 2025 PatSnap. All rights reserved.Legal|Privacy policy|Modern Slavery Act Transparency Statement|Sitemap|About US| Contact US: help@patsnap.com