Box Die Cutting Machine
A die-cutting machine and packing box technology, applied in metal processing, etc., can solve the problems of incoherent film conveying, affecting production efficiency, inconvenient operation, etc., and achieve high processing efficiency, good die-cutting effect and simple structure
- Summary
- Abstract
- Description
- Claims
- Application Information
AI Technical Summary
Problems solved by technology
Method used
Image
Examples
Embodiment Construction
[0023] Such as Figure 1-10As shown, a packaging box die-cutting machine includes a feeding mechanism, a conveying mechanism, a die-cutting mechanism, and a discharging mechanism arranged in sequence along the input to output direction, and grippers are arranged between the die-cutting mechanism and the discharging mechanism. The gripper row mechanism includes a driving wheel and a driven wheel. The driving wheel and the driven wheel are driven by a chain. The chain is evenly distributed with a gripper row. The lower part of the driving wheel and the lower part of the driven wheel are equipped with open teeth device, the die-cutting mechanism is located at the lower rear side of the driving wheel, and the unloading mechanism is located under the teeth opening device at the lower part of the driven wheel.
[0024] In this embodiment, the feeding mechanism includes a horizontal working platform for placing the film stack, a frame is arranged above the working platform, and a fil...
PUM
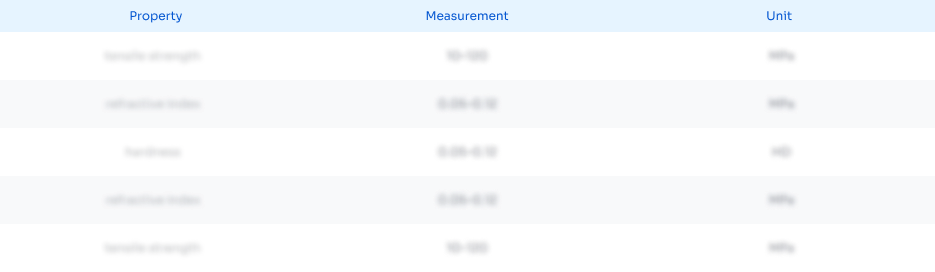
Abstract
Description
Claims
Application Information

- R&D
- Intellectual Property
- Life Sciences
- Materials
- Tech Scout
- Unparalleled Data Quality
- Higher Quality Content
- 60% Fewer Hallucinations
Browse by: Latest US Patents, China's latest patents, Technical Efficacy Thesaurus, Application Domain, Technology Topic, Popular Technical Reports.
© 2025 PatSnap. All rights reserved.Legal|Privacy policy|Modern Slavery Act Transparency Statement|Sitemap|About US| Contact US: help@patsnap.com