Ultra-deep vertical shaft winding type hoisting steel cable multi-axial friction fatigue damage monitoring device and method
A technology of damage monitoring and friction fatigue, which is applied in the directions of measuring devices, adopting mechanical devices, testing wear resistance, etc., can solve the problems that dynamic stretching, multi-axis friction fatigue and dynamic contact characteristics cannot be realized, and achieve the effect of wide application
- Summary
- Abstract
- Description
- Claims
- Application Information
AI Technical Summary
Problems solved by technology
Method used
Image
Examples
Embodiment Construction
[0027] The present invention will be further explained below in conjunction with the accompanying drawings.
[0028] Such as Figures 1 to 6 As shown, an ultra-deep vertical shaft winding hoisting wire rope multi-axis friction fatigue damage monitoring device of the present invention includes a support system, a tension-torsion fatigue system and a dynamic loading monitoring system.
[0029]The support system includes a bottom plate 24 , a friction lining support 21 , a friction lining 20 , a servo electric cylinder B support 11 , and a servo electric cylinder A support 18 . The friction lining 20 and the servo electric cylinder B bracket 11 are fixed on the friction lining bracket 21 , and the friction lining bracket 21 and the servo electric cylinder A bracket 18 are fixed on the bottom plate 24 .
[0030] The pull-torsion fatigue system includes a low-speed high-torque motor 1, a coupling A2, a torque sensor 3, a coupling B4, a shaft 5, a wire rope clamp A7, a wire rope U-...
PUM
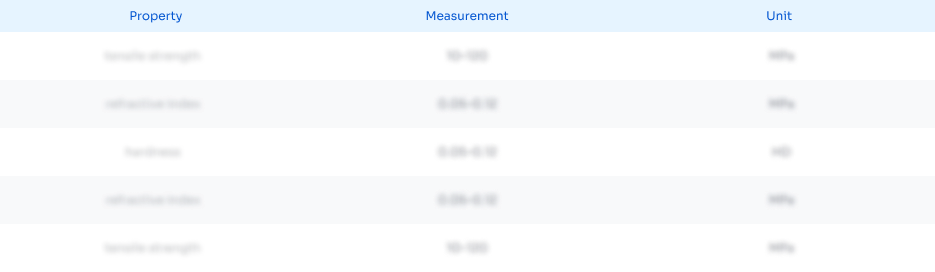
Abstract
Description
Claims
Application Information

- R&D Engineer
- R&D Manager
- IP Professional
- Industry Leading Data Capabilities
- Powerful AI technology
- Patent DNA Extraction
Browse by: Latest US Patents, China's latest patents, Technical Efficacy Thesaurus, Application Domain, Technology Topic, Popular Technical Reports.
© 2024 PatSnap. All rights reserved.Legal|Privacy policy|Modern Slavery Act Transparency Statement|Sitemap|About US| Contact US: help@patsnap.com