Forming method for insulating foam floor panel
A molding method and floor board technology, applied in the field of building material molding process, can solve the problems of roughness, complexity, the efficiency, strength and quality of molding products need to be improved, and achieve good quality, enhanced welding strength and quality, novel and reasonable process. Effect
- Summary
- Abstract
- Description
- Claims
- Application Information
AI Technical Summary
Problems solved by technology
Method used
Image
Examples
no. 1 approach
[0041] A kind of forming method of thermal insulation foam floor board of the present invention, such as figure 1 and 2 As shown, the first embodiment includes the following steps:
[0042] (1) Prepare the forming mold (not shown in the figure), use the manipulator to put the two C-shaped steel reinforcement bars of the floor plate into the forming mold, and ensure that the two ends of the C-shaped steel reinforcement stick out of the forming mold; (2) Use The manipulator flips one of the C-shaped steel reinforcements, so that the opening directions of the two C-shaped steel reinforcements are opposite, and uses the manipulator to position; (3) Clamp the forming mold; (4) Preheat the C-shaped steel reinforcement; (5) Vacuumize the forming mold, and gradually inject raw material particles into the forming mold while gradually vacuuming; (6) Form the floor board and open the mold to take the finished product. The invention utilizes a manipulator to realize mechanized operation...
no. 2 approach
[0043] The second embodiment includes the following steps:
[0044] (1) Prepare the forming mold (not shown in the figure), use the manipulator to put the two C-shaped steel reinforcement bars of the floor plate into the forming mold, and ensure that the two ends of the C-shaped steel reinforcement stick out of the forming mold; (2) Use The manipulator flips one of the C-shaped steel reinforcements, so that the opening directions of the two C-shaped steel reinforcements are opposite, and uses the manipulator to position; (3) Clamp the forming mold; (4) Preheat the C-shaped steel reinforcement; (5) Vacuumize the forming mold, and then inject the raw material particles into the forming mold after vacuuming; (6) Form the floor board and open the mold to take the finished product. The invention utilizes a manipulator to realize mechanized operation, and has good turning and positioning effects, high efficiency, safety and reliability; preheating the C-shaped steel reinforcing rib ...
PUM
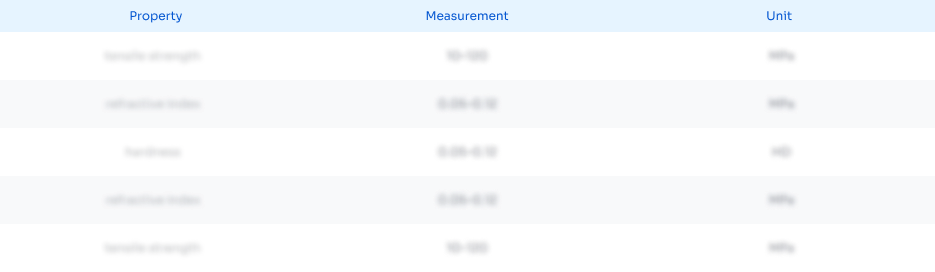
Abstract
Description
Claims
Application Information

- Generate Ideas
- Intellectual Property
- Life Sciences
- Materials
- Tech Scout
- Unparalleled Data Quality
- Higher Quality Content
- 60% Fewer Hallucinations
Browse by: Latest US Patents, China's latest patents, Technical Efficacy Thesaurus, Application Domain, Technology Topic, Popular Technical Reports.
© 2025 PatSnap. All rights reserved.Legal|Privacy policy|Modern Slavery Act Transparency Statement|Sitemap|About US| Contact US: help@patsnap.com