Electric control hydraulic damping cylinder structure for intelligent knee joint
An electronically controlled hydraulic, knee joint technology, applied in medical science, prosthesis, etc., can solve the problems of many connecting rods, difficult to process and manufacture, complicated holes, etc., and achieve the structure weight reduction, power consumption reduction, continuous damping adjustment Effect
- Summary
- Abstract
- Description
- Claims
- Application Information
AI Technical Summary
Problems solved by technology
Method used
Image
Examples
Embodiment Construction
[0019] The present invention will be described in detail below in conjunction with the accompanying drawings.
[0020] Such as figure 1 As shown, the present invention provides an electronically controlled hydraulic damping cylinder structure for intelligent knee joints, which includes an upper piston part 2 with a hollow piston rod and an upper piston block 11 with a hole, placed on the upper piston part 2 The upward-opening check valve 9 and the downward-opening check valve 4 in the hole of the upper piston block 11 are placed in the hollow piston rod of the piston part 2 and are directly connected to the upper stepping motor 1 through the valve core rod. shaped valve plate 10, the lower piston part 6 with the lower piston rod and the lower piston block 12 with holes, the cylinder body 5 of the opening, the cylinder cover 3 connected to the opening of the cylinder body, the spring case connected with the lower end of the cylinder body 5 8, the spring 7 placed in the spring ...
PUM
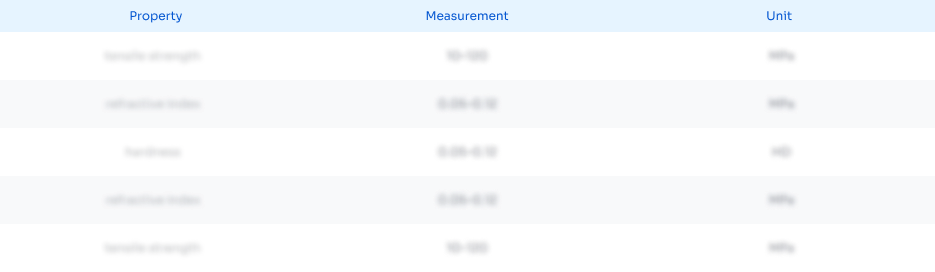
Abstract
Description
Claims
Application Information

- Generate Ideas
- Intellectual Property
- Life Sciences
- Materials
- Tech Scout
- Unparalleled Data Quality
- Higher Quality Content
- 60% Fewer Hallucinations
Browse by: Latest US Patents, China's latest patents, Technical Efficacy Thesaurus, Application Domain, Technology Topic, Popular Technical Reports.
© 2025 PatSnap. All rights reserved.Legal|Privacy policy|Modern Slavery Act Transparency Statement|Sitemap|About US| Contact US: help@patsnap.com