Casting mold and positioning method for setting auxiliary positioning device for vertical sand core
An auxiliary positioning and sand core technology, which is applied in the direction of casting mold, casting mold composition, mold box, etc., can solve the problems of rubbing sand on the head of the core, failure of the sand core to go in, poor fusion of the core support and the casting, etc., so as to avoid rubbing sand effect
- Summary
- Abstract
- Description
- Claims
- Application Information
AI Technical Summary
Problems solved by technology
Method used
Image
Examples
Embodiment Construction
[0017] The technical solution of the present invention and its implementation effects will be further described below in conjunction with the accompanying drawings.
[0018] see figure 1 , the casting mold with the above-mentioned vertical sand core auxiliary positioning device includes an upper box 1, a lower box 2, a main sand core 3, a vertical sand core 4, a positioning part 5, the upper sand mold in the upper box 1 and the lower box 2 The lower sand mold is provided with a cavity for accommodating the main sand core 3 and the vertical sand core 4. The vertical sand core 4 includes a lower core head 41 and a Lu core head 42. The upper core head 11 matched with the core head 42, the lower core head 21 matched with the lower core head 41 is set at the position where the lower sand mold and the lower core head 41 are facing each other, and the vertical sand core 4 is biased toward the pre-tilted side along the center of gravity Set the positioning piece 5, the positioning pi...
PUM
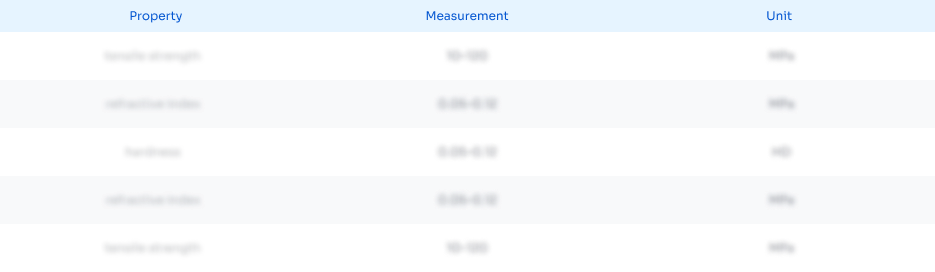
Abstract
Description
Claims
Application Information

- Generate Ideas
- Intellectual Property
- Life Sciences
- Materials
- Tech Scout
- Unparalleled Data Quality
- Higher Quality Content
- 60% Fewer Hallucinations
Browse by: Latest US Patents, China's latest patents, Technical Efficacy Thesaurus, Application Domain, Technology Topic, Popular Technical Reports.
© 2025 PatSnap. All rights reserved.Legal|Privacy policy|Modern Slavery Act Transparency Statement|Sitemap|About US| Contact US: help@patsnap.com