Part gripping device with self-checking function
A technology for grasping devices and parts, applied in manipulators, program-controlled manipulators, manufacturing tools, etc., can solve problems such as delayed work progress, unstable gripping, and lack of fault self-checking capabilities of the grasping device, and achieve stable grasping. Effect
- Summary
- Abstract
- Description
- Claims
- Application Information
AI Technical Summary
Problems solved by technology
Method used
Image
Examples
Embodiment 1
[0018] Such as figure 1 As shown, the present invention includes a base 1, and also includes a support member 2 installed on the base 1, a first arm 5, a second arm 6, a third arm 7, a grasping claw 9, a tray 14 and an auxiliary arm 15, The first arm 5, the second arm 6 and the third arm 7 are sequentially connected in series, and one end of the first arm 5 is also installed on the top of the support member 2, and one end of the third arm 7 is also connected with a grasping claw 9; The inside of described support member 2 is also provided with interconnected controller 4 and acquisition card, motor 3 is also installed on the outer wall of support member 2, camera 8 is also installed on the top of first arm 5, motor 3, camera 8 and the second The three arms 7 are all connected to the controller 4; the grabbing claw 9 is provided with a sliding grabbing plate 10 and a chute 11, and the sliding grabbing plate 10 can slide back and forth on the chute 11, at the bottom of the third...
Embodiment 2
[0021] This embodiment is preferably as follows on the basis of Embodiment 1: a layer of sponge is arranged inside the tray 14 . The setting of the sponge inside the tray can provide a buffer force on the contact surface between the large parts and the tray, avoiding collisions between the parts and the tray, resulting in damage to the parts.
[0022] A plurality of anti-slip blocks 12 are also arranged on the inner wall of the sliding grab board 10 . With the anti-slip fast setting, the friction between the gripping claw and the parts can be increased, further preventing the parts from slipping during the grabbing process, and preventing the parts from being damaged during the grabbing process.
[0023] The camera 8 can rotate at any angle of 360°. The design of the camera can facilitate the camera to adjust the angle to take pictures of parts with the best angle.
[0024] A plurality of ventilation holes are also provided on the side of the support member 2 . The ventilat...
PUM
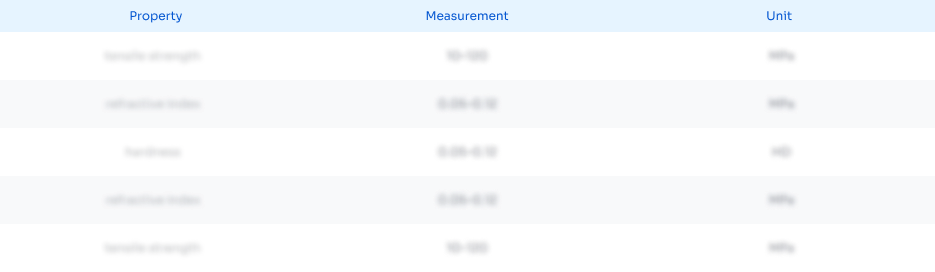
Abstract
Description
Claims
Application Information

- R&D Engineer
- R&D Manager
- IP Professional
- Industry Leading Data Capabilities
- Powerful AI technology
- Patent DNA Extraction
Browse by: Latest US Patents, China's latest patents, Technical Efficacy Thesaurus, Application Domain, Technology Topic, Popular Technical Reports.
© 2024 PatSnap. All rights reserved.Legal|Privacy policy|Modern Slavery Act Transparency Statement|Sitemap|About US| Contact US: help@patsnap.com