Forging method for maraging steel disc-shaft integrated forged piece
A maraging steel and forging technology, applied in the field of forging, can solve the problems of unqualified strength and plasticity index, difficult heating process of forgings, coarse grains of forgings, etc. , The effect of reducing the number of forming fires
- Summary
- Abstract
- Description
- Claims
- Application Information
AI Technical Summary
Problems solved by technology
Method used
Examples
Embodiment Construction
[0013] The present invention will be further described in detail below through specific embodiments:
[0014] The material for the low-pressure turbine shaft forging of a certain type of aeroengine is C250 ultra-high-strength steel. The length of the forging is 2115mm, the diameter of the disc is φ410mm, the diameter of the rod is φ150, the weight of the forging is 370Kg, and the blanking weight is 413Kg.
[0015] The heating temperature of the forging is 1040℃, and the final forging temperature of the forging is set to 750℃. After the bar is kept for 100 minutes, it is quickly wrapped with insulation cotton. After the wrapping, it is heated to the temperature holding time. After heating, it is upset in a special tire mold. , After finishing the upsetting, quickly take out the forgings and wrap the plate with insulation cotton, clamp the plate to lengthen the rod, and continuously use the pre-prepared long insulation cotton to cover the forging to ensure pressure deformation In the...
PUM
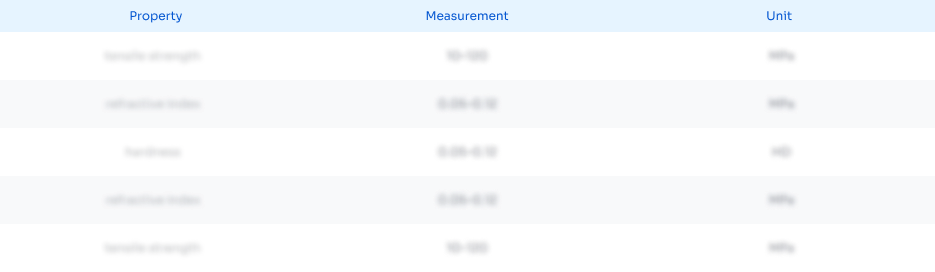
Abstract
Description
Claims
Application Information

- Generate Ideas
- Intellectual Property
- Life Sciences
- Materials
- Tech Scout
- Unparalleled Data Quality
- Higher Quality Content
- 60% Fewer Hallucinations
Browse by: Latest US Patents, China's latest patents, Technical Efficacy Thesaurus, Application Domain, Technology Topic, Popular Technical Reports.
© 2025 PatSnap. All rights reserved.Legal|Privacy policy|Modern Slavery Act Transparency Statement|Sitemap|About US| Contact US: help@patsnap.com