High-pressure-resistant washing system with multiple mechanical seals
A mechanical seal and flushing system technology, applied in the direction of mechanical equipment, machines/engines, liquid fuel engines, etc., can solve problems such as centrifugal pumps not being able to withstand high pressure, centrifugal pumps not working properly, centrifugal pumps leaking, etc., to achieve pressure bearing The effect of increased force, small footprint, and low production cost
- Summary
- Abstract
- Description
- Claims
- Application Information
AI Technical Summary
Problems solved by technology
Method used
Image
Examples
Embodiment Construction
[0055] The high-pressure flushing system with multiple sets of mechanical seals of the present invention will be described in detail below with reference to the embodiments and the accompanying drawings.
[0056] Such as Figure 5 , Figure 6 As shown, the high-pressure flushing system with multiple sets of mechanical seals of the present invention includes a centrifugal pump composed of a pump casing 7, an impeller 6 arranged in the pump casing 7, and a pump shaft 1 connected to the impeller 6 at one end. The other end of the pump shaft 1 extends out of the pump casing 7 through the high-pressure end mechanical seal 4 arranged on the shaft outlet hole of the pump casing 7, and the end is connected to the motor 10 for driving the impeller 6 to rotate through a coupling 9. The end of the pump shaft 1 connected to the shaft coupling 9 is positioned through the bearing 11 arranged on the bearing seat 8, and the outside of the pump shaft 1 is covered with a shaft sleeve 2, and th...
PUM
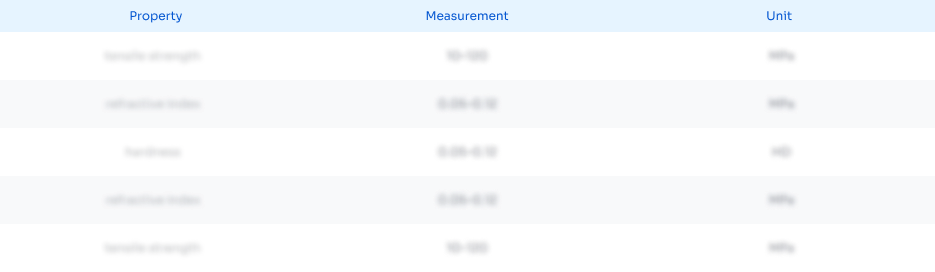
Abstract
Description
Claims
Application Information

- R&D
- Intellectual Property
- Life Sciences
- Materials
- Tech Scout
- Unparalleled Data Quality
- Higher Quality Content
- 60% Fewer Hallucinations
Browse by: Latest US Patents, China's latest patents, Technical Efficacy Thesaurus, Application Domain, Technology Topic, Popular Technical Reports.
© 2025 PatSnap. All rights reserved.Legal|Privacy policy|Modern Slavery Act Transparency Statement|Sitemap|About US| Contact US: help@patsnap.com