Large-scale motor casing machining technology
A processing technology, a technology for large motors, applied in the manufacture of motor generators, electrical components, electromechanical devices, etc., can solve the problems of difficult to operate verticality, inaccuracy, low production efficiency, etc., to improve production efficiency and production quality, positioning Accurate, easy-to-use results
- Summary
- Abstract
- Description
- Claims
- Application Information
AI Technical Summary
Problems solved by technology
Method used
Image
Examples
Embodiment Construction
[0020] Embodiments of the present invention are further described below in conjunction with accompanying drawings:
[0021] Such as figure 1 and figure 2 As shown, a large motor housing is processed through the following process steps:
[0022] (1), use TPX6111 boring and milling machine to roughly mill the first end face 5 of the motor housing;
[0023] (2) Use the inner hole 4 of the first end of the motor casing for positioning, and use the C5123 vertical lathe to roughly turn the second end face 1 and the second end inner hole 2 of the motor casing;
[0024] (3), using the second end inner hole 2 of the motor housing for positioning, use a C5123 vertical lathe to roughly turn the first end face 5 of the motor housing, the first end inner hole 4 and the middle hole 3;
[0025] (4), use TPX6111 boring and milling machine to rough mill the foot surface 6;
[0026] (5), drill the end face holes of the first end face 4 and the second end face 1 with a drill press;
[0027...
PUM
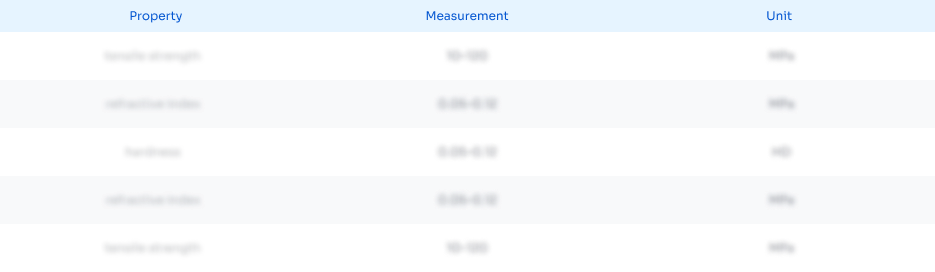
Abstract
Description
Claims
Application Information

- Generate Ideas
- Intellectual Property
- Life Sciences
- Materials
- Tech Scout
- Unparalleled Data Quality
- Higher Quality Content
- 60% Fewer Hallucinations
Browse by: Latest US Patents, China's latest patents, Technical Efficacy Thesaurus, Application Domain, Technology Topic, Popular Technical Reports.
© 2025 PatSnap. All rights reserved.Legal|Privacy policy|Modern Slavery Act Transparency Statement|Sitemap|About US| Contact US: help@patsnap.com