Image collection device for correction of dual-camera module and application method of image collection device
A dual-camera, image acquisition technology, applied in photography, image analysis, image communication, etc., can solve the problem of inability to guarantee the parallelism of the optical axes of the two cameras, and achieve the effect of improving the quality of imaging images
- Summary
- Abstract
- Description
- Claims
- Application Information
AI Technical Summary
Problems solved by technology
Method used
Image
Examples
Embodiment Construction
[0028] The present invention will be described in detail below in conjunction with the accompanying drawings and embodiments.
[0029] Please refer to figure 1 , which shows an image acquisition device for dual camera module calibration in a preferred embodiment of the present invention, which includes:
[0030] A rack (not shown in the figure);
[0031] An image acquisition mechanism 1, which is arranged on the front side of the frame; the image acquisition mechanism 1 includes a carrier plate fixedly installed on the front side of the frame and at least one set of waiting Correct the dual camera module 11;
[0032] Has the first chart figure 2 The first adjustment mechanism (not shown in the figure), which is located on the rear side of the image acquisition mechanism 1 and is arranged on the frame, is used to provide different first distances 21 and / or Or the first chart of the first deflection angle 22 figure 2 , implement the first chart figure 2 Relative to the ...
PUM
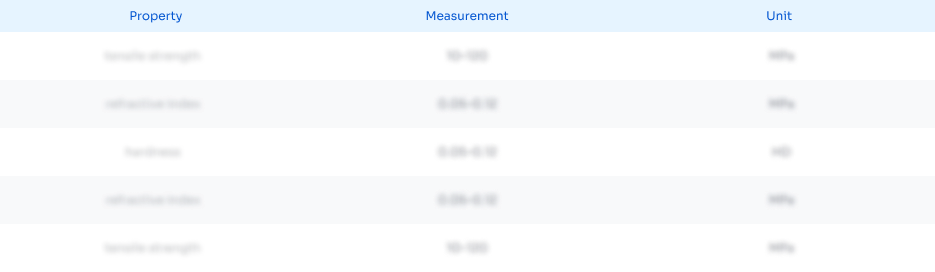
Abstract
Description
Claims
Application Information

- R&D Engineer
- R&D Manager
- IP Professional
- Industry Leading Data Capabilities
- Powerful AI technology
- Patent DNA Extraction
Browse by: Latest US Patents, China's latest patents, Technical Efficacy Thesaurus, Application Domain, Technology Topic, Popular Technical Reports.
© 2024 PatSnap. All rights reserved.Legal|Privacy policy|Modern Slavery Act Transparency Statement|Sitemap|About US| Contact US: help@patsnap.com