Accuracy measurement method for precision tapered hole
A technology of precision measurement and taper hole, which is applied in the direction of angle/taper measurement, measuring device, mechanical measuring device, etc. It can solve the problems that the taper angle and large end diameter of the workpiece cannot be measured online, the taper angle cannot be measured online, etc. , to achieve the effects of simplifying the processing and testing process, improving efficiency, and simple and reliable structure
- Summary
- Abstract
- Description
- Claims
- Application Information
AI Technical Summary
Problems solved by technology
Method used
Image
Examples
Embodiment 1
[0035] Such as Figures 1 to 6 As shown, a precision measuring device for taper holes is composed of a dial gauge 1, a gauge base 2, a standard pad 3, a taper plug gauge 4 and a standard ring gauge 10. The gauge base 2 is a cylinder, and the gauge base 2 passes through a cross Slotted countersunk head screw 5 is fixed on the upper surface of standard pad 3 and table base 2 and standard pad 3 are concentric, the center of table base 2 and standard pad 3 has a center hole, and taper plug gauge 4 is located between table base 2 and standard pad 3 In the center hole of the table seat 2 and the standard pad 3 away from the end of the screw 5 and in a position symmetrical to the screw 5, a through hole 7 is opened, the lower part of the dial gauge 1 is fixed in the through hole 7 and the dial gauge 7 The contact is flush with the lower surface of the standard pad; the standard ring gauge 10 is set as a separate component. When testing, the measuring part of the taper plug gauge 4 is...
PUM
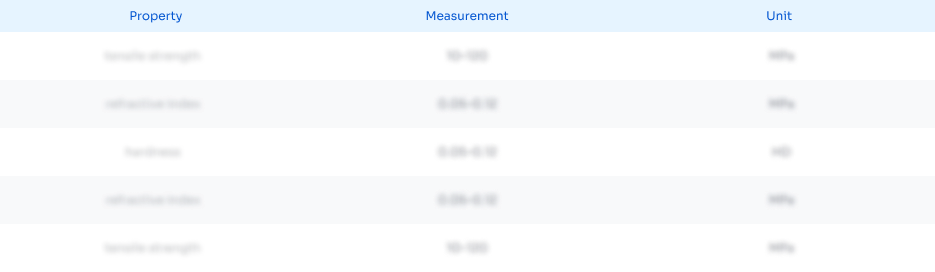
Abstract
Description
Claims
Application Information

- R&D Engineer
- R&D Manager
- IP Professional
- Industry Leading Data Capabilities
- Powerful AI technology
- Patent DNA Extraction
Browse by: Latest US Patents, China's latest patents, Technical Efficacy Thesaurus, Application Domain, Technology Topic, Popular Technical Reports.
© 2024 PatSnap. All rights reserved.Legal|Privacy policy|Modern Slavery Act Transparency Statement|Sitemap|About US| Contact US: help@patsnap.com