Four-degree-of-freedom posture leveling mechanism
A technology of leveling mechanism and degree of freedom, applied in manipulators, program-controlled manipulators, manufacturing tools, etc., can solve the problem that the vibration reduction effect cannot satisfy the crew, etc., and achieve the effect of relatively simple kinematics, simple control, and concise structure
- Summary
- Abstract
- Description
- Claims
- Application Information
AI Technical Summary
Problems solved by technology
Method used
Image
Examples
Embodiment 1
[0017] Such as figure 1 A four-degree-of-freedom attitude leveling mechanism is shown, including a quadrilateral moving platform 5, a quadrilateral fixed platform 6, and four branch chains connecting the corresponding corners of the moving platform 5 and the fixed platform 6. The first branch chain 1 includes sequentially connected balls Vice 11, the first connecting rod 12, the first Hooke pair 13, the first driving block 14, the first moving pair 15 and the first square column 16, the second branch chain 2 includes the second Hooke pair 21, The second connecting rod 22, the second rotating pair 23, the second driving block 24, the second moving pair 25 and the second square column 26, the first square column 16, the column 19 and the second square column 25 are respectively fixed on the fixed platform 6 On the corner of the upper surface, the ball pair 11 and the second Hooke pair 21 are respectively connected to a corner of the moving platform 5, the first branch chain 1 an...
Embodiment 2
[0023] Such as figure 2 A four-degree-of-freedom attitude leveling mechanism is shown, including a quadrilateral moving platform 5, a quadrilateral fixed platform 6, and four branch chains connecting the corresponding corners of the moving platform 5 and the fixed platform 6. The first branch chain 1 includes sequentially connected balls Vice 11, first connecting rod 12, first rotating pair 17, first driving block 14, cylinder pair 18 and cylinder 19, the second branch chain 2 includes the second Hooke pair 21, the second connecting rod 22, The second rotating pair 23, the second driving block 24, the second moving pair 25 and the second square post 26, the first square post 16, the post 19 and the second square post 25 are respectively fixed on the corners of the upper surface of the fixed platform 6, The ball pair 11 and the second Hooke pair 21 are respectively connected to one corner of the moving platform 5, the first branch chain 1 and the third branch chain 3 have the ...
PUM
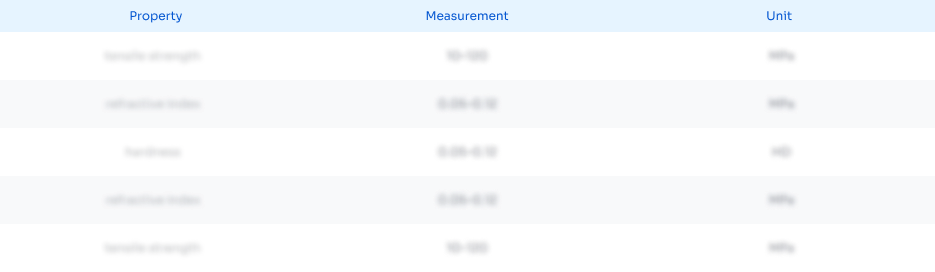
Abstract
Description
Claims
Application Information

- R&D
- Intellectual Property
- Life Sciences
- Materials
- Tech Scout
- Unparalleled Data Quality
- Higher Quality Content
- 60% Fewer Hallucinations
Browse by: Latest US Patents, China's latest patents, Technical Efficacy Thesaurus, Application Domain, Technology Topic, Popular Technical Reports.
© 2025 PatSnap. All rights reserved.Legal|Privacy policy|Modern Slavery Act Transparency Statement|Sitemap|About US| Contact US: help@patsnap.com