Loading device and method for measuring micro-vibration characteristics of structures
A loading device and micro-vibration technology, which is used in measurement devices, machine/structural component testing, vibration testing, etc., can solve problems such as increasing loading instability and control difficulty, and inability to achieve vibration.
- Summary
- Abstract
- Description
- Claims
- Application Information
AI Technical Summary
Problems solved by technology
Method used
Image
Examples
Embodiment 1
[0025] Example as figure 1 , 3 , 4, the loading device for measuring the amplitude-frequency characteristic curve of the test piece under low-acceleration vibration according to the present invention includes: computer 1, data acquisition system 3, piezoelectric ceramic controller 2, laser vibrometer 4, elastic rope 5 and piezoelectric ceramics 7, wherein the test piece 6 is suspended on the aluminum frame of the vibrating table through the elastic rope 5, and the piezoelectric ceramics 7 is pasted on the surface excitation input end of the test piece 6 and connected with the output end of the piezoelectric ceramic controller 2 Connected, the excitation control system includes: computer 1, data acquisition system 3, piezoelectric ceramic controller 2 and piezoelectric ceramics 7, wherein computer 1 is connected to data acquisition system 3, and the frequency sweep output terminal of data acquisition system 3 is connected to piezoelectric ceramics The input end of the ceramic ...
Embodiment 2
[0034] Example two such as figure 2 , 3 As shown, the difference between the second embodiment and the first embodiment is that two identical piezoelectric ceramics 7 are pasted on the test piece 6, and the piezoelectric ceramic controller applies an anti-phase control voltage to the two piezoelectric ceramics, thereby The amplitude-frequency characteristic curve under the condition that a moment load is applied to the test piece 6 can be obtained.
PUM
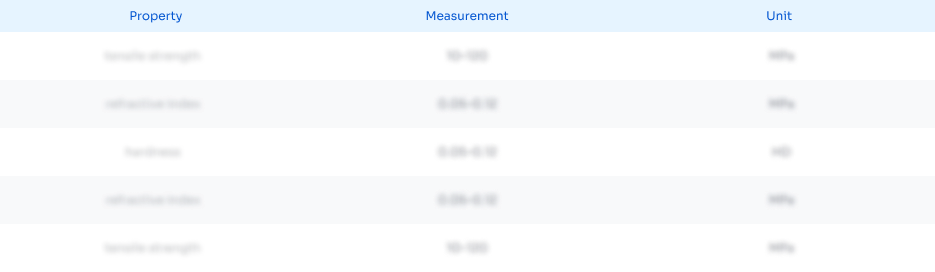
Abstract
Description
Claims
Application Information

- Generate Ideas
- Intellectual Property
- Life Sciences
- Materials
- Tech Scout
- Unparalleled Data Quality
- Higher Quality Content
- 60% Fewer Hallucinations
Browse by: Latest US Patents, China's latest patents, Technical Efficacy Thesaurus, Application Domain, Technology Topic, Popular Technical Reports.
© 2025 PatSnap. All rights reserved.Legal|Privacy policy|Modern Slavery Act Transparency Statement|Sitemap|About US| Contact US: help@patsnap.com