Travelling crane positioning control system and control method
A positioning control and controller technology, applied in two-dimensional position/channel control, control drive, electric vehicles, etc., can solve the problem of high labor cost, achieve the effects of reduced labor cost, high stability, and low wear
- Summary
- Abstract
- Description
- Claims
- Application Information
AI Technical Summary
Problems solved by technology
Method used
Image
Examples
Embodiment Construction
[0031] Such as Figures 1 to 2As shown, an embodiment of the control system of the present invention includes a brake 1, a traveling frequency converter 2 and a traveling motor 3, the output ends of the brake 1 and the traveling motor 3 are connected to the driving 4, and the output terminals of the traveling frequency converter 2 Linked to the input end of the travel motor 3, also includes
[0032] The distance positioning sensor 5 is used to measure the actual distance y traveled by the vehicle 4;
[0033] Driving controller 6, described driving controller 6 comprises seeking difference module 8, first selection unit 9, acceleration controller 11, deceleration controller 7, braking controller 10, the output terminal of distance positioning sensor 5 and seeking module 8 is connected to the input end, the output end of the difference module 8 is connected to the input end of the brake controller 10 and the first selection unit 9 respectively, the output end of the brake contr...
PUM
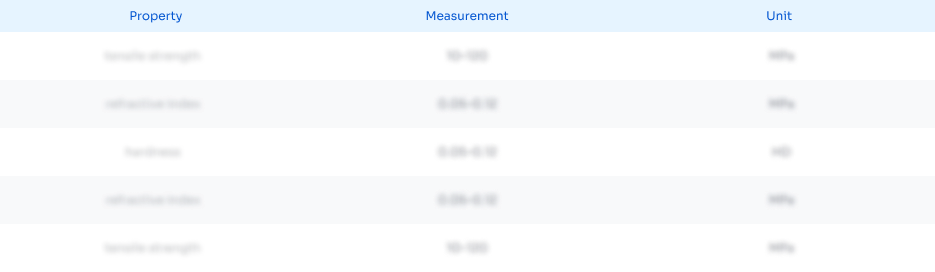
Abstract
Description
Claims
Application Information

- R&D
- Intellectual Property
- Life Sciences
- Materials
- Tech Scout
- Unparalleled Data Quality
- Higher Quality Content
- 60% Fewer Hallucinations
Browse by: Latest US Patents, China's latest patents, Technical Efficacy Thesaurus, Application Domain, Technology Topic, Popular Technical Reports.
© 2025 PatSnap. All rights reserved.Legal|Privacy policy|Modern Slavery Act Transparency Statement|Sitemap|About US| Contact US: help@patsnap.com