Control method for automatic guided vehicle (AGA)
A control method and trolley technology, which are applied to conveyor control devices, conveyors, conveyor objects, etc., can solve problems such as inconvenient control and low efficiency of AGV systems, and achieve the effect of reducing labor intensity and realizing industrial automation.
- Summary
- Abstract
- Description
- Claims
- Application Information
AI Technical Summary
Problems solved by technology
Method used
Image
Examples
Embodiment Construction
[0027] The present invention will be further described below in conjunction with the accompanying drawings.
[0028] refer to figure 1 and figure 2 As shown, the control method of the AGV trolley of the present invention, the control method is applied to the AGV trolley system, the AGV trolley system includes an AGV trolley, a docking truss, and the AGV trolley includes a vehicle frame 1, a yarn fetching mechanism 2 and a yarn setting platform 4, and the vehicle frame 1 One end of the vehicle frame 1 is provided with a yarn-taking mechanism 2, and the other end of the vehicle frame 1 is provided with a yarn-setting platform 4. The yarn-taking mechanism 2 is set on one side of the yarn-setting platform 4. The docking truss includes a bracket 40, an X-axis guide rail 10, and a Y-axis guide rail. 20. Z-axis guide rail 30, grabbing mechanism 301 and assembly line 50, Y-axis guide rail 20 is set on bracket 40, X-axis guide rail 10 is set on Y-axis guide rail 20, Z-axis guide rail...
PUM
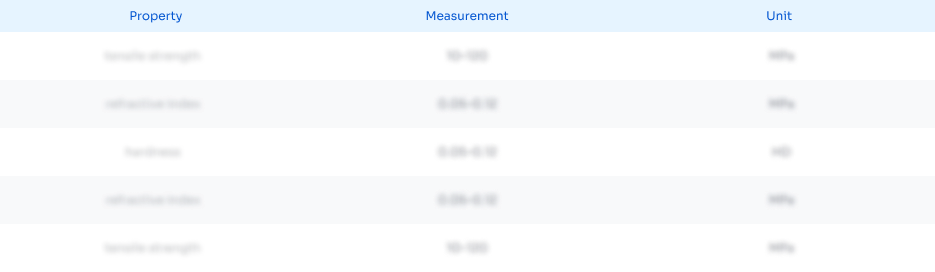
Abstract
Description
Claims
Application Information

- Generate Ideas
- Intellectual Property
- Life Sciences
- Materials
- Tech Scout
- Unparalleled Data Quality
- Higher Quality Content
- 60% Fewer Hallucinations
Browse by: Latest US Patents, China's latest patents, Technical Efficacy Thesaurus, Application Domain, Technology Topic, Popular Technical Reports.
© 2025 PatSnap. All rights reserved.Legal|Privacy policy|Modern Slavery Act Transparency Statement|Sitemap|About US| Contact US: help@patsnap.com