Coaxial assembly method for shaft components and coaxiality detection method for shaft components
A technology of assembly method and detection method, applied in the direction of assembly machine, measuring device, using optical device, etc., can solve the problem of inability to assist coaxial assembly and coaxiality detection, and achieve improved assembly product efficiency, high speed, and reduced processing. cost effect
- Summary
- Abstract
- Description
- Claims
- Application Information
AI Technical Summary
Problems solved by technology
Method used
Image
Examples
Embodiment 1
[0029] In this embodiment, the shafting parts that need to be assembled coaxially are the shafting parts at both ends of the U-shaped seat, and its structural characteristics are as follows figure 1 As shown: the two sides of the U-shaped seat 3 are the left and right half-shaft parts (denoted as the left shaft part 1 and the right shaft part 2) connected by the middle frame. First, ensure that the two shaft parts rotate coaxially, so that the middle frame can Coaxial rotation in two shaft systems.
[0030] The coaxial assembly method of shafting components in this embodiment includes the following steps:
[0031] 1) Confirm that the bearing installation shafts of the two shafting components to be coaxially assembled have process holes, and the coaxiality between the axis of the process holes and the bearing installation shaft is not greater than 0.02mm;
[0032] Such as figure 1 As shown, the inner focusing telescope 4 and the U-shaped seat 3 are placed on the fixed platfor...
Embodiment 2
[0038] In this embodiment, the shafting parts at both ends of the assembled U-shaped seat are tested. The structural characteristics of the shafting parts at both ends of the U-shaped seat are as follows: figure 1As shown: the two sides of the U-shaped seat 3 are the left and right half-shaft parts (denoted as the left shaft part 1 and the right shaft part 2) connected by the middle frame, and the two shaft parts rotate coaxially (axis 5 such as figure 1 shown), in order to make the middle frame rotate coaxially in the two shaft systems.
[0039] The method for detecting the coaxiality of shafting components in this embodiment includes the following steps:
[0040] 1) Confirm that the bearing installation shafts of the two shafting components that have been coaxially assembled have process holes, and the coaxiality between the axis of the process holes and the bearing installation shaft is not greater than 0.02mm;
[0041] Such as figure 1 As shown, the inner focusing telesc...
PUM
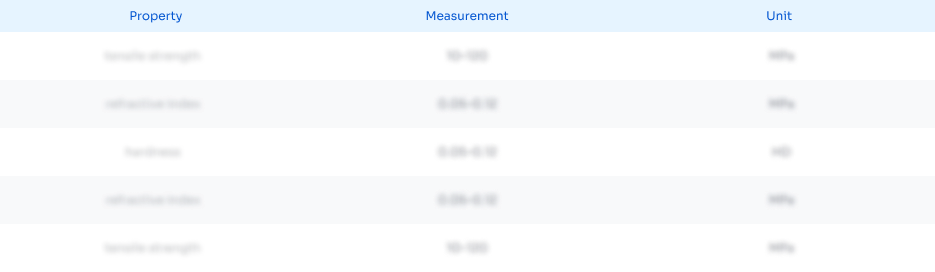
Abstract
Description
Claims
Application Information

- R&D
- Intellectual Property
- Life Sciences
- Materials
- Tech Scout
- Unparalleled Data Quality
- Higher Quality Content
- 60% Fewer Hallucinations
Browse by: Latest US Patents, China's latest patents, Technical Efficacy Thesaurus, Application Domain, Technology Topic, Popular Technical Reports.
© 2025 PatSnap. All rights reserved.Legal|Privacy policy|Modern Slavery Act Transparency Statement|Sitemap|About US| Contact US: help@patsnap.com