Stamping dies with tolerance compensation
A stamping forming and mold technology, applied in the direction of presses, forming tools, manufacturing tools, etc., can solve the problems of cooling performance decline, small cooling rate, etc.
- Summary
- Abstract
- Description
- Claims
- Application Information
AI Technical Summary
Problems solved by technology
Method used
Image
Examples
Embodiment Construction
[0034] figure 1 A side cross-sectional view of a press forming die 101 according to the present invention is shown. For this purpose, the stamping tool 101 has a pressure punch 102 , shown from top to bottom in the plane of the drawing, to which an upper die 103 , not shown in detail, is coupled. The stamping force F is applied by the press punch 102 in the vertical direction V, which simultaneously corresponds to the stamping stroke movement, and the upper die 103 and the lower die 104 are closed. Between the upper die 103 and the lower die 104 there remains an inter-die space 105 and a slab not shown in detail in the figure, which, within the scope of the invention, is particularly preferably in full contact with the corresponding mold surfaces 106, 107 . According to the invention it is provided that a tool clamping plate 109 is arranged on the stamping table 108 and that different elastic adjustment elements 110 are arranged between the lower tool 104 and the tool clampi...
PUM
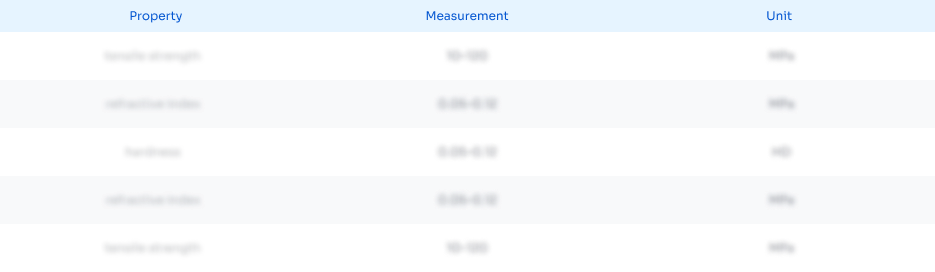
Abstract
Description
Claims
Application Information

- R&D
- Intellectual Property
- Life Sciences
- Materials
- Tech Scout
- Unparalleled Data Quality
- Higher Quality Content
- 60% Fewer Hallucinations
Browse by: Latest US Patents, China's latest patents, Technical Efficacy Thesaurus, Application Domain, Technology Topic, Popular Technical Reports.
© 2025 PatSnap. All rights reserved.Legal|Privacy policy|Modern Slavery Act Transparency Statement|Sitemap|About US| Contact US: help@patsnap.com