A method for manufacturing a low-speed flutter wind tunnel model of an airfoil
A manufacturing method and wing technology, applied in computer-aided design, instruments, geometric CAD, etc., can solve the problems of unfavorable aerodynamic shape accurate simulation, affecting test accuracy, inconvenient installation and testing, etc., and achieve accurate and accurate geometric shape simulation. , the effect of high structural efficiency
- Summary
- Abstract
- Description
- Claims
- Application Information
AI Technical Summary
Problems solved by technology
Method used
Image
Examples
Embodiment Construction
[0030] In the proposal of this application, a method for manufacturing a low-speed flutter wind tunnel model of an airfoil includes the following steps:
[0031] A method for manufacturing a wing low-speed flutter wind tunnel model, comprising the following steps:
[0032] Step 1) adopt energy method or single closed chamber profile method to extract the stiffness distribution and mass distribution of original wing;
[0033] Step 2) Select an appropriate length scaling ratio and velocity scaling ratio according to the target wind tunnel parameters, and calculate the stiffness scaling ratio and mass scaling ratio according to the similarity criterion;
[0034] Step 3) Obtain the target stiffness distribution and the target mass distribution of the flutter model according to the stiffness distribution and mass distribution and the stiffness scaling ratio and the mass scaling ratio of the original wing;
[0035] Step 4) Determine the parameters of the composite material flutter ...
PUM
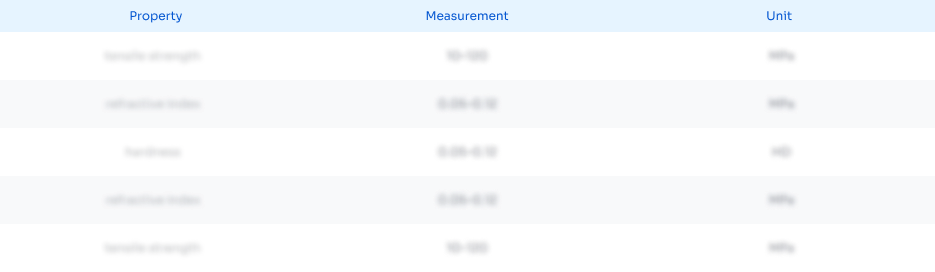
Abstract
Description
Claims
Application Information

- Generate Ideas
- Intellectual Property
- Life Sciences
- Materials
- Tech Scout
- Unparalleled Data Quality
- Higher Quality Content
- 60% Fewer Hallucinations
Browse by: Latest US Patents, China's latest patents, Technical Efficacy Thesaurus, Application Domain, Technology Topic, Popular Technical Reports.
© 2025 PatSnap. All rights reserved.Legal|Privacy policy|Modern Slavery Act Transparency Statement|Sitemap|About US| Contact US: help@patsnap.com