Continuous technology for producing polycarboxylate superplasticizer monomer polyether through one-step method
A monomer polyether and polycarboxylic acid technology, applied in the field of polyether synthesis, can solve the problems of long production cycle, affecting product quality, quality fluctuation, etc., to improve production efficiency and product yield, and reduce the difficulty of process and operation , Improve the effect of product quality stability
- Summary
- Abstract
- Description
- Claims
- Application Information
AI Technical Summary
Problems solved by technology
Method used
Examples
Embodiment 1
[0030] The continuous method synthesis of four reactors with a molecular weight of methacryl alcohol polyoxyethylene ether of 2400:
[0031] ①Put 360kg of methacrylic alcohol and 14kg of flake potassium hydroxide into the 3m3 reactor A, use high-purity N2 to replace the air in the reactor three times, then vacuum pump to below -0.095MPa, heat the reactor to 85°C, slowly Feed ethylene oxide into the reactor at a uniform speed to make up to 0.05MPa. After the material in the reactor initiates the reaction to release heat, the temperature of the reactor is slowly raised to 90° C., and then 1390 kg of ethylene oxide is introduced into the reactor. Control the reaction temperature T=95-105°C, and the reaction pressure P<0.10MPa. After feeding, keep the temperature T=95-105°C for 0.5h under reduced pressure, and then import all the materials into the 6m3 reactor B.
[0032] ②After the A kettle is poured, continue to repeat the production process of the A kettle. At the same time, ...
Embodiment 2
[0037] The continuous synthesis of prenol polyoxyethylene ether with a molecular weight of 2000 by four reactors:
[0038] ①Put 430kg of isopentenol and 21kg of flake sodium hydroxide into the 3m3 reactor A, replace the air in the reactor with high-purity N2 three times, then vacuum pump to below -0.095MPa, heat the reactor to 85°C, and slowly Feed ethylene oxide into the reactor at a uniform speed to make up to 0.05MPa. After the material in the reactor initiates the reaction to release heat, the temperature of the reactor is slowly raised to 90° C., and then 1100 kg of ethylene oxide is introduced into the reactor. Control the reaction temperature T=95-105°C, and the reaction pressure P<0.10MPa. After feeding, keep the temperature T=95-105°C for 0.5h under reduced pressure, and then import all the materials into the 6m3 reactor B.
[0039]②After the A kettle is poured, continue to repeat the production process of the A kettle. At the same time, material in the B kettle beg...
Embodiment 3
[0043] Embodiment 3: four reaction kettles continuous method synthetic molecular weight is the tetrahydroxybutyl vinyl polyoxyethylene ether of 4000:
[0044] ①Put 355kg of tetrahydroxybutyl vinyl ether and 35kg of sodium hydride into the 3m3 reactor A, use high-purity N2 to replace the air in the reactor three times, then vacuum pump to below -0.095MPa, heat the reactor to 85°C, and slowly Feed ethylene oxide into the reactor at a uniform speed to make up to 0.05MPa. After the material in the reactor initiates the reaction to release heat, the temperature of the reactor is slowly raised to 90° C., and then 1536 kg of ethylene oxide is introduced into the reactor. Control the reaction temperature T=95-105°C, and the reaction pressure P<0.10MPa. After feeding, keep the temperature T=95-105°C for 0.5h under reduced pressure, and then import all the materials into the 6m3 reactor B.
[0045] ②After the A kettle is poured, continue to repeat the production process of the A kettle...
PUM
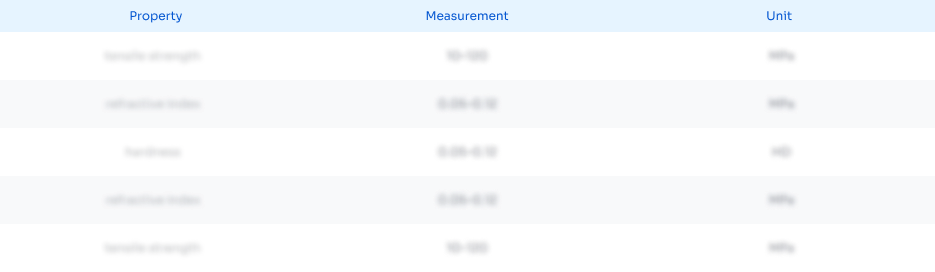
Abstract
Description
Claims
Application Information

- R&D
- Intellectual Property
- Life Sciences
- Materials
- Tech Scout
- Unparalleled Data Quality
- Higher Quality Content
- 60% Fewer Hallucinations
Browse by: Latest US Patents, China's latest patents, Technical Efficacy Thesaurus, Application Domain, Technology Topic, Popular Technical Reports.
© 2025 PatSnap. All rights reserved.Legal|Privacy policy|Modern Slavery Act Transparency Statement|Sitemap|About US| Contact US: help@patsnap.com