Man-machine interaction system for chassis height adjustment control and control method
A technology of human-computer interaction and height adjustment, applied in general control system, control/adjustment system, test/monitoring control system, etc., can solve the problems of mismatch between control method and control system, lack of high-precision control system, etc., and achieve simplicity And real-time guidance, precise and controllable height adjustment work, and visualization effects
- Summary
- Abstract
- Description
- Claims
- Application Information
AI Technical Summary
Problems solved by technology
Method used
Image
Examples
Embodiment Construction
[0058] Specific embodiments of the present invention will be described in detail below in conjunction with the accompanying drawings.
[0059] Such as figure 1 As shown, this embodiment includes a system signal interaction device 01 connected to a CAN bus controller 11 for data communication with the corresponding CAN bus controller 11, and the working condition of the actuator controlled by the CAN bus controller 11 The data is converted into graphic data and output to the signal interaction device, and the input graphic data is converted into control data and output to the CAN bus controller 11;
[0060] These include:
[0061] The processor 12 is used for data communication with the CAN bus controller 11, reading working condition data from the data packet, and writing control data into the data packet;
[0062] A reading module 13, configured to request working condition data from the processor 12 according to built-in rules, and output the working condition data;
[0063...
PUM
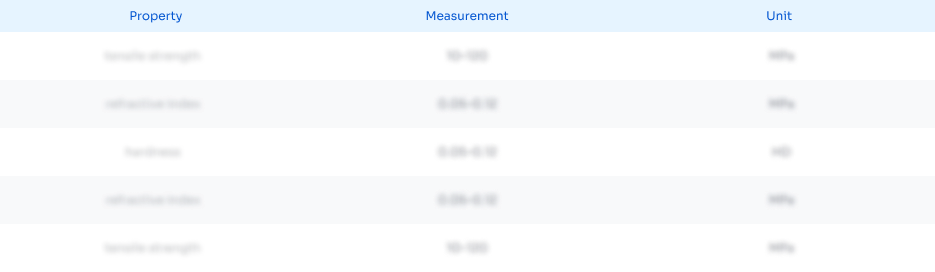
Abstract
Description
Claims
Application Information

- R&D
- Intellectual Property
- Life Sciences
- Materials
- Tech Scout
- Unparalleled Data Quality
- Higher Quality Content
- 60% Fewer Hallucinations
Browse by: Latest US Patents, China's latest patents, Technical Efficacy Thesaurus, Application Domain, Technology Topic, Popular Technical Reports.
© 2025 PatSnap. All rights reserved.Legal|Privacy policy|Modern Slavery Act Transparency Statement|Sitemap|About US| Contact US: help@patsnap.com