Docking measurement pose-adjusting method based on indoor GPS (iGPS)
A technology of attitude adjustment and measuring points, which is applied in the direction of aircraft parts, metal processing, metal processing equipment, etc., can solve the problems of affecting assembly efficiency, low docking efficiency, inability to integrate application of data management system, assembly drive equipment, etc., to improve docking The effect of quality and efficiency
- Summary
- Abstract
- Description
- Claims
- Application Information
AI Technical Summary
Problems solved by technology
Method used
Image
Examples
Embodiment Construction
[0033] Preferred embodiments of the present disclosure will be described in more detail below with reference to the accompanying drawings. Although preferred embodiments of the present disclosure are shown in the drawings, it should be understood that the present disclosure may be embodied in various forms and should not be limited to the embodiments set forth herein. Rather, these embodiments are provided so that this disclosure will be thorough and complete, and will fully convey the scope of the disclosure to those skilled in the art.
[0034] Compared with traditional measurement equipment such as laser trackers, iGPS measurement equipment is especially suitable for large-scale measurement. It has the advantages of large measurement range, multi-point simultaneous measurement, and good real-time measurement, which can realize the overall monitoring of the entire aircraft section pose and adjust.
[0035] In order to illustrate the concept of the present invention, the win...
PUM
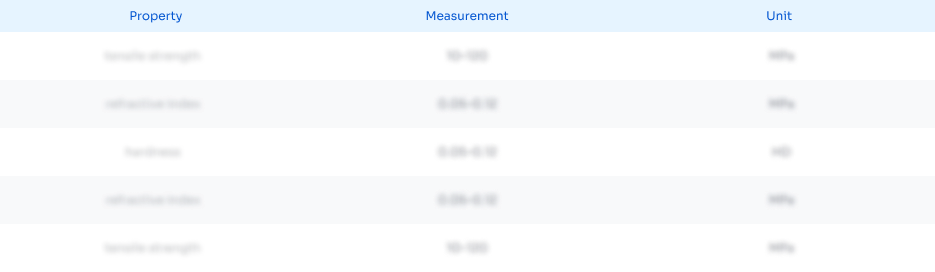
Abstract
Description
Claims
Application Information

- R&D
- Intellectual Property
- Life Sciences
- Materials
- Tech Scout
- Unparalleled Data Quality
- Higher Quality Content
- 60% Fewer Hallucinations
Browse by: Latest US Patents, China's latest patents, Technical Efficacy Thesaurus, Application Domain, Technology Topic, Popular Technical Reports.
© 2025 PatSnap. All rights reserved.Legal|Privacy policy|Modern Slavery Act Transparency Statement|Sitemap|About US| Contact US: help@patsnap.com