Mould used on reconstituted bamboo lumber mould pressing production line
A production line and material mold technology, used in household appliances, other household appliances, wood processing appliances, etc., can solve the problems of high labor intensity, weight increase, low work efficiency, etc., to reduce labor intensity, simple operation, and improve work efficiency. Effect
- Summary
- Abstract
- Description
- Claims
- Application Information
AI Technical Summary
Problems solved by technology
Method used
Image
Examples
Embodiment 1
[0038] The U-shaped base groove structure of this embodiment is as follows: Figure 4 shown.
[0039] The structure of the side plate bump head 111 and the side plate bump connection portion 112 is a square structure, the top edge of the side plate bump head 111, the top edge of the side plate bump connection portion 112 and the top edge of the side plate are A straight line, the bottom edge of the side plate bump head 111 is located below the bottom edge of the side plate bump connection portion 112 , that is, the height of the side plate bump head 111 is greater than the height of the side plate bump connection portion 112 .
[0040] The front edge of the side plate bump head is provided with a pin half-hole 151 for installing the pin, and the front edge of the side plate groove 12 is also provided with a pin that cooperates with the side plate bump head pin half hole 151 to form an integral pin hole. Pillar and a half hole; the front single-mode upper side plate groove 12 ...
Embodiment 2
[0047] The difference between this embodiment and Embodiment 1 is that the cross-sectional structure of the bottom plate bump hook 131 is circular, such as Figure 7 shown.
Embodiment 3
[0049] The difference between this embodiment and Embodiment 1 is that the cross-sectional structure of the hook head 131 of the bottom plate bump is trapezoidal, the width of the front end of the hook head 131 of the bottom plate bump is greater than the width of the rear end, and the width of the rear end of the hook head 131 of the bottom plate bump is the same as that of the bottom plate convex hook head 131. Block connection blocks 132 are of equal width, such as Figure 10 with Figure 11 shown.
[0050] In this embodiment, the contact surface between the support block 141 in the groove of the bottom plate and the hook head 131 of the bottom plate bump is a stepped surface with a high front end and a low rear end, as shown in Figure 8 , Figure 10 with Figure 11 shown.
[0051] The three single molds described in this embodiment are used to assemble the mold, and the mold structure after splicing is as follows Figure 8 with Figure 9 shown.
PUM
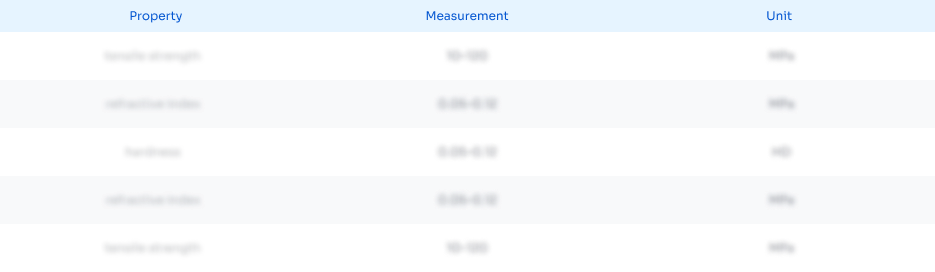
Abstract
Description
Claims
Application Information

- R&D
- Intellectual Property
- Life Sciences
- Materials
- Tech Scout
- Unparalleled Data Quality
- Higher Quality Content
- 60% Fewer Hallucinations
Browse by: Latest US Patents, China's latest patents, Technical Efficacy Thesaurus, Application Domain, Technology Topic, Popular Technical Reports.
© 2025 PatSnap. All rights reserved.Legal|Privacy policy|Modern Slavery Act Transparency Statement|Sitemap|About US| Contact US: help@patsnap.com