Clamp for machining of dish-cover type parts
A part processing and jig technology, which is applied in the field of jigs for the processing of disc cover parts, can solve the problems of unfavorable production efficiency and complicated processes, and achieve the effect of improving the flexibility of use and the pressing range.
- Summary
- Abstract
- Description
- Claims
- Application Information
AI Technical Summary
Problems solved by technology
Method used
Image
Examples
Embodiment Construction
[0015] In order to make the technical means and creative features realized by the present invention easy to understand, the present invention will be further elaborated below.
[0016] Such as Figure 1 to Figure 4 As shown, a fixture for processing disc cover parts includes a base plate 1, on which a positioning column 2 is arranged, and a number of movable pressing devices 3 are distributed around the base plate 1, and the movable pressing devices 3 include main Bracket 4, the lower end of the main bracket 4 is equipped with a rotating connecting column 5, and a circumferential groove 6 is provided on the rotating connecting column 5, and the upper end of the main bracket 4 is connected with a pressure frame 7 in a hinged manner. Stage clip 8 is installed on the outer lower part of press frame 7, and the other end of described stage clip 8 is installed on the main support 4, and the inner side lower end surface of described press frame 7 is evenly provided with tooth groove ...
PUM
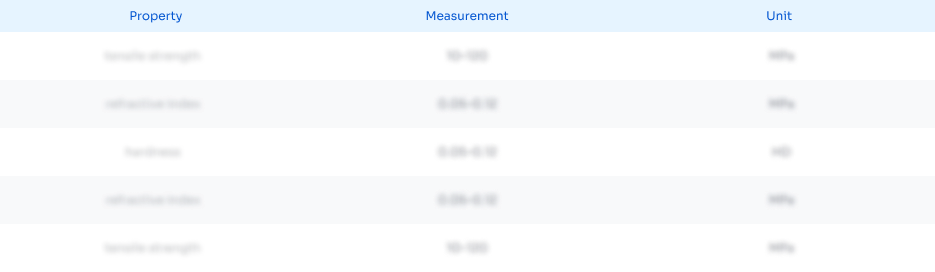
Abstract
Description
Claims
Application Information

- R&D
- Intellectual Property
- Life Sciences
- Materials
- Tech Scout
- Unparalleled Data Quality
- Higher Quality Content
- 60% Fewer Hallucinations
Browse by: Latest US Patents, China's latest patents, Technical Efficacy Thesaurus, Application Domain, Technology Topic, Popular Technical Reports.
© 2025 PatSnap. All rights reserved.Legal|Privacy policy|Modern Slavery Act Transparency Statement|Sitemap|About US| Contact US: help@patsnap.com