All-attitude three-frame four-axis inertial platform servo ring control method
A control method and technology of the follow-up ring, applied in the direction of using feedback control, navigation through speed/acceleration measurement, etc., can solve the problems of abnormal operation of the platform system, loss of normal function, and cannot exceed ±45°, etc., to achieve the elimination of angle Restrict, realize full posture work, overcome the effect of working dead zone
- Summary
- Abstract
- Description
- Claims
- Application Information
AI Technical Summary
Problems solved by technology
Method used
Image
Examples
Embodiment Construction
[0023] For the convenience of description, the definition of the frame coordinate system of the four-axis inertial platform is given first, such as figure 1 As shown, the OX' axis is the follower axis, and the rotation angle range is -180° to +180°; the OX axis is the inner ring axis, and the rotation angle range is -45° to +45°; the OY axis is the outer ring axis, and the rotation angle range is -180° to +180°; OZ axis is the platform axis, and the rotation angle range is -180° to +180°; OXpYpZp is the platform coordinate system; OX'XYZ is the platform frame axis system. define theta x' Indicates the angle of the follower axis, and the polarity is defined as the positive rotation output of the platform base around the OX’ axis, and the positive rotation direction conforms to the right-hand rule; θ y Indicates the angle of the outer ring axis, and the polarity is defined as the positive rotation output of the platform following the OY axis, and the positive rotation direction...
PUM
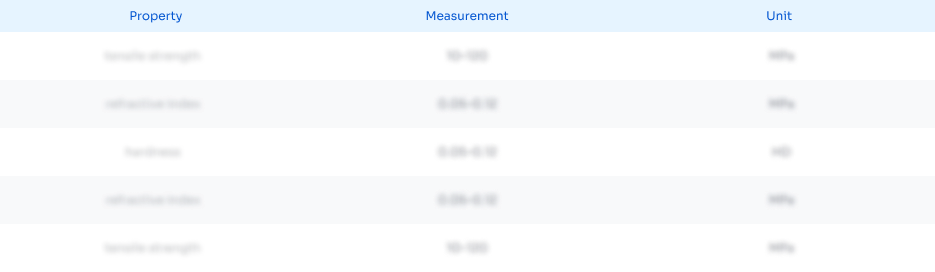
Abstract
Description
Claims
Application Information

- R&D
- Intellectual Property
- Life Sciences
- Materials
- Tech Scout
- Unparalleled Data Quality
- Higher Quality Content
- 60% Fewer Hallucinations
Browse by: Latest US Patents, China's latest patents, Technical Efficacy Thesaurus, Application Domain, Technology Topic, Popular Technical Reports.
© 2025 PatSnap. All rights reserved.Legal|Privacy policy|Modern Slavery Act Transparency Statement|Sitemap|About US| Contact US: help@patsnap.com