Method for producing lithium carbonate by separating magnesium out of low-lithium bittern and enriching lithium
A lithium carbonate, brine technology, applied in separation methods, chemical instruments and methods, lithium carbonate;/acid carbonate, etc., can solve problems such as limitations, no breakthrough changes in solvent extraction technology, etc. Enhanced extraction ability, improved lithium-magnesium separation ability, and high metal ion extraction rate
- Summary
- Abstract
- Description
- Claims
- Application Information
AI Technical Summary
Problems solved by technology
Method used
Image
Examples
Embodiment 1
[0029] Li in the old brine of a salt lake in Qaidam Basin, Qinghai + , Mg 2+ and The contents are 2.24, 118.00 and 39.87g / L respectively, and the mass ratio of magnesium to lithium is equal to 52.58. Take 350mL of the old brine in a 1000mL beaker, heat and concentrate it on a temperature-adjusting electric furnace, and evaporate the water accounting for 25% of the total mass of the old brine. After cooling, all the liquid will be precipitated and transformed into a brine salt containing crystal water. Transfer to a mechanically stirred container, add 354.5mL trihexyl phosphate to it, the solid-liquid mass volume ratio is equal to 1:1 (g / mL), and carry out solid-liquid extraction at room temperature for 30min. Subsequently, the solid-liquid mixture was moved into a sand core funnel for suction filtration under reduced pressure to obtain the organic extract phase of the filtrate and the remaining halogen salt. Heat the remaining brine salt until it is completely dissolved, a...
Embodiment 2
[0036] Get 350mL of the old brine from the salt lake in Example 1 in a 1000mL beaker, and add therein the LiCl H with an analytically pure content of 97%. 2 O11.49g, the mass ratio of magnesium to lithium in the mixture is equal to 20.00. Heating and concentrating on a temperature-adjusting electric furnace evaporates 25% of the water that accounts for the total mass of the initial old brine, and after cooling, all the liquid is precipitated and transformed into a brine salt containing crystal water. Transfer to a mechanically stirred container, add 366.8mL trihexyl phosphate to it, the solid-liquid mass volume ratio is equal to 1:1 (g / mL), and carry out solid-liquid extraction at room temperature for 30min. Subsequently, the solid-liquid mixture was moved into a sand core funnel for suction filtration under reduced pressure to obtain the organic extract phase of the filtrate and the remaining halogen salt. Heat the remaining brine salt until it is completely dissolved, and t...
Embodiment 3
[0042] Take 350 mL of the old brine from the salt lake in Example 1 in a 1000 mL beaker, and the mass ratio of magnesium to lithium is equal to 52.58. Heating and concentrating on a temperature-adjusting electric furnace evaporates the water accounting for 25% of the total mass of the old brine, and after cooling, all the liquid is precipitated and transformed into a brine salt containing crystal water. Transfer to a mechanically stirred container, add 354.7mL tributyl phosphate to it, the solid-liquid mass volume ratio is equal to 1:1 (g / mL), and carry out solid-liquid extraction at room temperature for 30min. Subsequently, the solid-liquid mixture was moved into a sand core funnel for suction filtration under reduced pressure to obtain the organic extract phase of the filtrate and the remaining halogen salt. Heat the remaining brine salt until it is completely dissolved, and then cool it to precipitate out, and obtain the brine salt containing crystal water for the second ti...
PUM
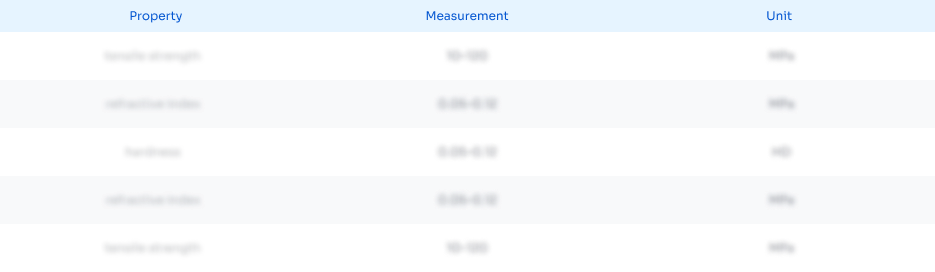
Abstract
Description
Claims
Application Information

- Generate Ideas
- Intellectual Property
- Life Sciences
- Materials
- Tech Scout
- Unparalleled Data Quality
- Higher Quality Content
- 60% Fewer Hallucinations
Browse by: Latest US Patents, China's latest patents, Technical Efficacy Thesaurus, Application Domain, Technology Topic, Popular Technical Reports.
© 2025 PatSnap. All rights reserved.Legal|Privacy policy|Modern Slavery Act Transparency Statement|Sitemap|About US| Contact US: help@patsnap.com