Tapered roller bearing pressing and assembling device
A technology of tapered roller bearing and press-fitting device is applied in the field of bearing press-fitting, which can solve the problems of large operating force, poor assembly accuracy, and difficulty in ensuring the concentricity between the tapered roller bearing and the shaft to be pressed, so as to improve the press-fitting. Accuracy, the effect of reducing work intensity
- Summary
- Abstract
- Description
- Claims
- Application Information
AI Technical Summary
Problems solved by technology
Method used
Image
Examples
Embodiment Construction
[0022] In order to enable those skilled in the art to better understand the technical solutions of the present invention, the present invention will be further described in detail below in conjunction with the accompanying drawings.
[0023] combined with Figure 2-4 As shown, the present invention provides a press-fitting device for tapered roller bearings. In order to solve the defects in the prior art, the present invention makes the following technical improvements: including a press, and the pressure action along the press The pressing rod 10, the pressing head 20 and the guide head 30 connected by the line in turn, the pressing rod 10 is fixedly connected to the press, the cavity 21 is arranged in the pressing head 20, the guiding head 30 is fixedly connected in the cavity 21 through the connecting rod 40, and Under the action of the spring force, the guide head 30 reciprocates along the pressure action line in the cavity 21. In the feeding state, the tapered roller bear...
PUM
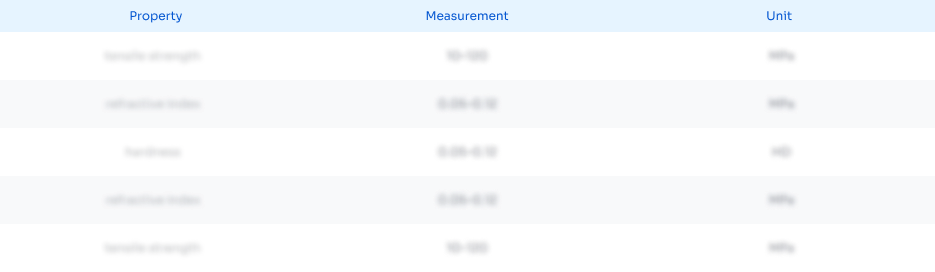
Abstract
Description
Claims
Application Information

- R&D
- Intellectual Property
- Life Sciences
- Materials
- Tech Scout
- Unparalleled Data Quality
- Higher Quality Content
- 60% Fewer Hallucinations
Browse by: Latest US Patents, China's latest patents, Technical Efficacy Thesaurus, Application Domain, Technology Topic, Popular Technical Reports.
© 2025 PatSnap. All rights reserved.Legal|Privacy policy|Modern Slavery Act Transparency Statement|Sitemap|About US| Contact US: help@patsnap.com