Core setting size control device and method for annular casting
A size control and ring-shaped technology, applied in the field of size control of the core setting process, can solve the problems of casting deformation, increase the process cost of mold making and molding process, and difficult to adjust the sand box, so as to prevent local deformation and misalignment, and simplify core setting The effect of operating process and shortening the core setting cycle
- Summary
- Abstract
- Description
- Claims
- Application Information
AI Technical Summary
Problems solved by technology
Method used
Image
Examples
Embodiment 1
[0019] like figure 1 As shown, the device for controlling the size of the lower core of an annular casting of the present invention includes a vertically arranged rotary shaft 1, a fixed seat 6 is provided at the bottom of the rotary shaft 1, a rotary bearing 2 is fixed on the rotary shaft 1, and the outer surface of the rotary bearing 2 The ring is fixedly provided with a connecting frame, the connecting frame is fixedly connected with a beam 3, the end of the beam 3 is fixedly connected with the vertical beam 4, and the lower part of the vertical beam 4 is fixedly connected with the clamping plate 5, and the shape of the clamping plate 5 is consistent with the radial profile of the annular casting cavity. adaptation. In order to further ensure the strength of the device, in this device, the crossbeam 3 is made of channel steel. For the convenience of installation and connection of the device, a number of installation holes are provided along the length direction of the cross...
Embodiment 2
[0022] like figure 2 and image 3 As shown, the method for controlling the size of the lower core of the annular casting by using the above-mentioned device of the present invention includes the following process: (a) according to the radius of gyration of the annular cavity of the annular casting, the device for controlling the size of the lower core of the annular casting is fixedly connected For each component, the radius of gyration of the inner and outer contours of the clamping plate 5 is respectively equal to the corresponding radius of gyration of the radial inner and outer sides of the annular cavity of the casting;
[0023] (b) Verify the position accuracy of the pallet: Take two detection points on the surface of the pallet 5, wherein the first detection point is located at the upper part of the radial inner side of the pallet 5, and the second detection point is located at the lower part of the radial outer side of the pallet 5. Revolving shaft 1 rotates crossbea...
PUM
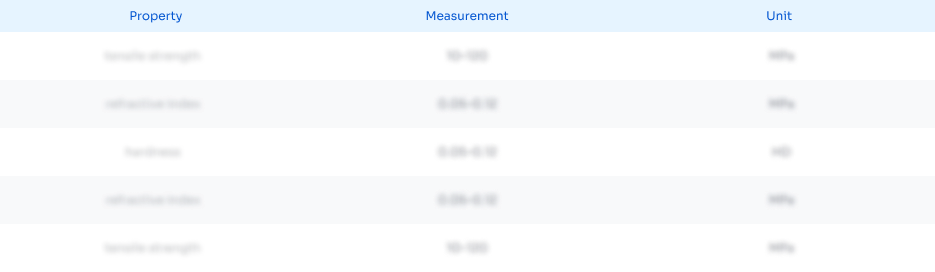
Abstract
Description
Claims
Application Information

- R&D
- Intellectual Property
- Life Sciences
- Materials
- Tech Scout
- Unparalleled Data Quality
- Higher Quality Content
- 60% Fewer Hallucinations
Browse by: Latest US Patents, China's latest patents, Technical Efficacy Thesaurus, Application Domain, Technology Topic, Popular Technical Reports.
© 2025 PatSnap. All rights reserved.Legal|Privacy policy|Modern Slavery Act Transparency Statement|Sitemap|About US| Contact US: help@patsnap.com