A scaling test method for ship ballast water treatment system
A technology of ship ballast water and treatment system, which is applied in the scale test field of ship ballast water treatment system, which can solve the problems of huge test seawater volume, many test and inspection items, and increase certification cost, so as to reduce the test preparation work The effect of reducing the amount of water, reducing the area of the test site, and reducing the amount of seawater
- Summary
- Abstract
- Description
- Claims
- Application Information
AI Technical Summary
Problems solved by technology
Method used
Image
Examples
Embodiment 1
[0055] Scale-scale certification test for Type A electrolysis ship ballast water treatment system. Measured in the test: salinity: 35PSU; electrolyzer flow rate: 17.1m3 / h, average TRO concentration at sampling point 1: 0.43mg / L, average TRO concentration at sampling point 2: 1223mg / L. Hydrogen content in the upper space of simulated ballast tank: 0%LEL.
[0056] Calculated according to formula (1): Chlorine production = (1223mg / L-0.43 mg / L) * 17.1 m3 / h / 1000 = 20.9kg / h.
[0057] Assuming that the minimum TRO concentration required by this type of ballast water treatment system to meet the requirements of D-2 is 4mg / L and the maximum treatment is 1200 m3 / h, the required minimum chlorine production is: 4mg / L * 1200 m3 / h=4.8kg / h.
[0058] Final verification result:
[0059] (1) The actual chlorine production measured by the verification test: 20.9kg / h > The theoretically required minimum chlorine production: 4.8kg / h; therefore, it can meet the IMO D-2 standard;
[0060] (2) H...
Embodiment 2
[0062] Scale-scale certification test for Type B electrolysis ship ballast water treatment system. Measured in the test: salinity: 26PSU; electrolyzer flow rate: 10.5m3 / h, average TRO concentration at sampling point 1: 0.35mg / L, average TRO concentration at sampling point 2: 1125mg / L. Hydrogen content in the upper space of simulated ballast tank: 0%LEL.
[0063] Calculated according to formula (1): Chlorine production = (1125mg / L-0.35 mg / L) * 10.5 m3 / h / 1000 = 11.8kg / h.
[0064] Assuming that the minimum TRO concentration required by this type of ballast water treatment system to meet the requirements of D-2 is 6mg / L and the maximum treatment is 800 m3 / h, the required minimum chlorine production is: 8mg / L * 800 m3 / h = 6.4kg / h.
[0065] Final verification result:
[0066] (1) The actual chlorine production measured by the verification test: 11.8kg / h > the theoretically required minimum chlorine production: 6.4kg / h; therefore, it can meet the IMO D-2 standard;
[0067] (2) M...
Embodiment 3
[0069] Scale certification test for Type C electrolysis ship ballast water treatment system. Measured in the test: salinity: 14.5PSU; electrolytic cell flow rate: 13.2m3 / h, average TRO concentration at sampling point 1: 0.33mg / L, average TRO concentration at sampling point 2: 989mg / L. Hydrogen content in the upper space of simulated ballast tank: 0%LEL.
[0070] Calculated according to formula (1): Chlorine production = (989mg / L – 0.33 mg / L) * 13.2 m3 / h / 1000 = 13.05kg / h.
[0071] Assuming that the minimum TRO concentration required by this type of ballast water treatment system to meet the requirements of D-2 is 9mg / L, and the maximum treatment is 1000 m3 / h, the required minimum chlorine production is: 9mg / L * 1000 m3 / h = 9kg / h.
[0072] Final verification result:
[0073] (1) The actual chlorine production measured by the verification test: 13.05kg / h > The theoretically required minimum chlorine production: 9kg / h; therefore, it can meet the IMO D-2 standard;
[0074] (2)...
PUM
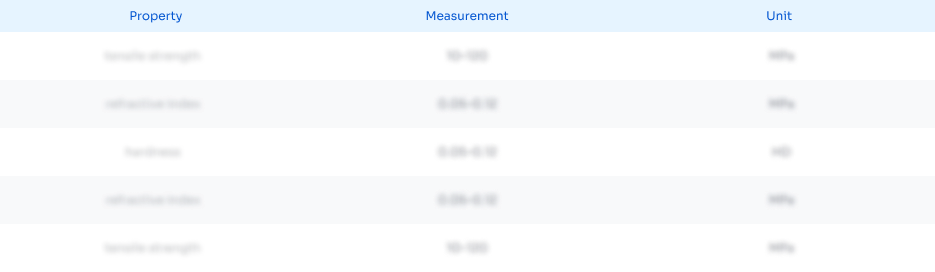
Abstract
Description
Claims
Application Information

- R&D
- Intellectual Property
- Life Sciences
- Materials
- Tech Scout
- Unparalleled Data Quality
- Higher Quality Content
- 60% Fewer Hallucinations
Browse by: Latest US Patents, China's latest patents, Technical Efficacy Thesaurus, Application Domain, Technology Topic, Popular Technical Reports.
© 2025 PatSnap. All rights reserved.Legal|Privacy policy|Modern Slavery Act Transparency Statement|Sitemap|About US| Contact US: help@patsnap.com