High-precision dynamic angle measuring device and method
A high-precision, angle-measuring technology, used in measuring devices, measuring angles, mapping and navigation, etc., can solve the problems of complex on-site debugging, small angle measurement range, and high assembly accuracy requirements, and achieve the best practical application value.
- Summary
- Abstract
- Description
- Claims
- Application Information
AI Technical Summary
Problems solved by technology
Method used
Image
Examples
Embodiment Construction
[0025] Below in conjunction with accompanying drawing, the present invention will be further described:
[0026] see figure 1 , which is the structure and components of the high-precision dynamic angle measuring device targeted by the present invention. The dynamic angle measurement device of the present invention includes a spatial four-frequency differential laser gyro 1, a flexible cable 2, a gyro control / demodulation circuit 3, a circular induction synchronizer 7, an induction synchronizer demodulation circuit 8, and an angle increment signal processing circuit 4, 422 A bus 5, and an angle measurement computer 10, wherein the spatial four-frequency differential laser gyroscope 1 is installed on the rotating shaft 9 to be measured via the transition plate 6, and the two are rigidly connected by screws or mechanical fastening devices. The transition plate 6 is made of stainless steel, which has the advantages of high hardness, good stability, non-magnetic conduction, etc., ...
PUM
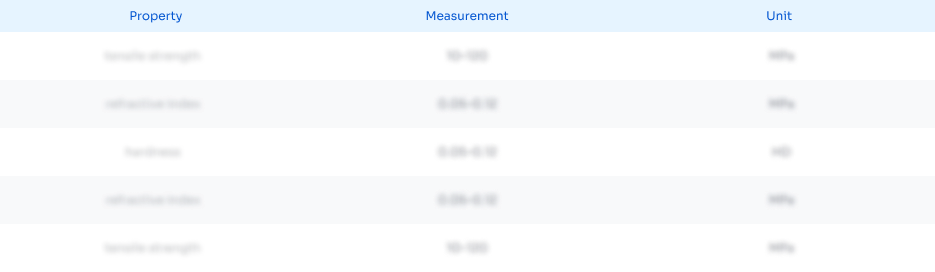
Abstract
Description
Claims
Application Information

- R&D
- Intellectual Property
- Life Sciences
- Materials
- Tech Scout
- Unparalleled Data Quality
- Higher Quality Content
- 60% Fewer Hallucinations
Browse by: Latest US Patents, China's latest patents, Technical Efficacy Thesaurus, Application Domain, Technology Topic, Popular Technical Reports.
© 2025 PatSnap. All rights reserved.Legal|Privacy policy|Modern Slavery Act Transparency Statement|Sitemap|About US| Contact US: help@patsnap.com