Material grabbing flexible gripper suitable for various structure styles
A structure type and material technology, applied in the direction of manipulators, chucks, manufacturing tools, etc., can solve the problems of reducing production efficiency and increasing costs, and achieve the effects of increased production efficiency, reduced production costs, and stable clamping force
- Summary
- Abstract
- Description
- Claims
- Application Information
AI Technical Summary
Problems solved by technology
Method used
Image
Examples
specific Embodiment approach 1
[0010] Embodiment 1: Combining Figure 1 to Figure 3 Describe this embodiment, a flexible hand gripper for picking and placing materials of various structural types in this embodiment, which includes a gripper assembly 1, a screw 2, a servo motor 3 and a support frame body 4, and the servo motor 3 is installed On one side of the lower end of the support frame body 4, the output end of the servo motor 3 is connected to one end of the lead screw 2, and the other end of the lead screw 2 is connected to the support frame body 4, and the jaw assembly 1 is movably installed on the lead screw assembly 2 on,
[0011] The jaw assembly 1 includes a left jaw 1-1 and a right jaw 1-2, the left jaw 1-1 and the right jaw 1-2 have the same structure, and the left jaw 1-1 and the right jaw 1-2 are symmetrical Staggered setting, the left jaw 1-1 includes claw body 1-3, frame plate 1-4, bracket 1-5, cylinder 1-6, suction cup 1-7 and lead screw nut 1-8, and claw body 1-3 The upper part is rotat...
specific Embodiment approach 2
[0014] Specific implementation mode 2: Combining Figure 1 to Figure 3 Describe this embodiment, the claw body 1-3 of this embodiment comprises claw body frame 1-3-1 and claw body 1-3-2, and the eccentric connection between claw body frame 1-3-1 and one end of cylinder 1-6, Claw 1-3-2 is fixedly installed on the claw body frame 1-3-1. With such arrangement, the upper right side of the claw body frame 1-3-1 is connected with the cylinder 1-6, which is convenient for connection and more concentrated in clamping force. Other compositions and connections are the same as in the first embodiment.
specific Embodiment approach 3
[0015] Specific implementation three: combination Figure 1 to Figure 3 Describe this embodiment, the claw frame 1-3-1 of this embodiment is a hollow claw frame, and the claw 1-3-2 is a hollow claw. Such arrangement reduces the overall weight of the gripper. Other compositions and connection relationships are the same as in the second embodiment.
PUM
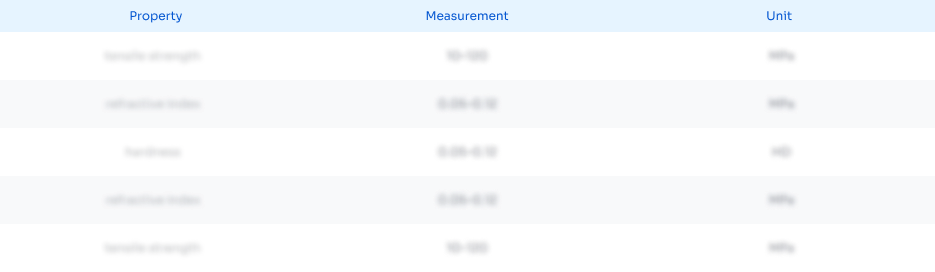
Abstract
Description
Claims
Application Information

- R&D
- Intellectual Property
- Life Sciences
- Materials
- Tech Scout
- Unparalleled Data Quality
- Higher Quality Content
- 60% Fewer Hallucinations
Browse by: Latest US Patents, China's latest patents, Technical Efficacy Thesaurus, Application Domain, Technology Topic, Popular Technical Reports.
© 2025 PatSnap. All rights reserved.Legal|Privacy policy|Modern Slavery Act Transparency Statement|Sitemap|About US| Contact US: help@patsnap.com