Simple mechanical arm
A manipulator and a simple technology, applied in the field of manipulators, can solve the problems of poor movement flexibility of the manipulator, influence of the work efficiency of the manipulator, and small range of motion of the manipulator, and achieve the effects of simple structure, low production cost and large range of motion.
- Summary
- Abstract
- Description
- Claims
- Application Information
AI Technical Summary
Problems solved by technology
Method used
Image
Examples
Embodiment Construction
[0065] The following are specific embodiments of the present invention and in conjunction with the accompanying drawings, the technical solutions of the present invention are further described, but the present invention is not limited to these embodiments.
[0066] Such as figure 1 As shown, a simple manipulator of the present invention includes a manipulator assembly 100 connected in sequence, a first control mechanism 200, a forearm 300, a second control mechanism 400, a third control mechanism 500, a main arm 600, a fourth control mechanism 700, a base Seat 800.
[0067] Such as figure 2 As shown, the manipulator assembly 100 includes a mounting base 110 and a pneumatic gripper 120 .
[0068] The mounting base 110 is triangular in shape and has two adjacent mounting surfaces and fixed surfaces adjacent to the two mounting surfaces respectively. The pneumatic gripper 120 is used to clamp and place the workpiece. Mounted on two mounting surfaces.
[0069] Such as image...
PUM
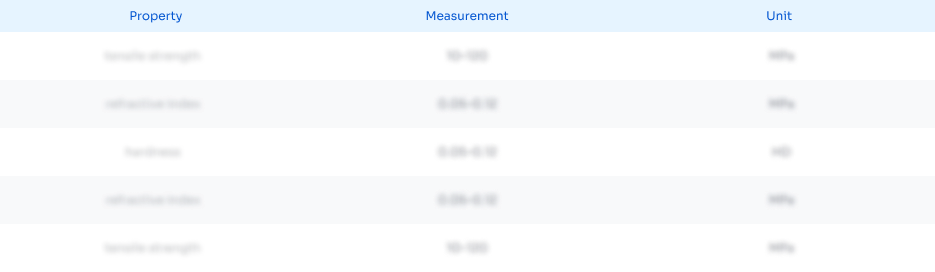
Abstract
Description
Claims
Application Information

- Generate Ideas
- Intellectual Property
- Life Sciences
- Materials
- Tech Scout
- Unparalleled Data Quality
- Higher Quality Content
- 60% Fewer Hallucinations
Browse by: Latest US Patents, China's latest patents, Technical Efficacy Thesaurus, Application Domain, Technology Topic, Popular Technical Reports.
© 2025 PatSnap. All rights reserved.Legal|Privacy policy|Modern Slavery Act Transparency Statement|Sitemap|About US| Contact US: help@patsnap.com