Automatic assembly system of spacecraft cabin on ground
An assembly system and spacecraft technology, applied to ground devices, aircraft assembly, transportation and packaging, etc., can solve problems such as low docking accuracy and poor stability
- Summary
- Abstract
- Description
- Claims
- Application Information
AI Technical Summary
Problems solved by technology
Method used
Image
Examples
specific Embodiment approach 1
[0075] Specific implementation mode one: combine figure 1 and figure 2 Describe this embodiment, illustrate this embodiment, the automatic assembly system of the spacecraft cabin described in this embodiment on the ground, the assembly system includes a master control system 4, a laser tracker 3 and a parallel mechanism 5;
[0076] The master control system 4 is used to control the laser tracker 3, and according to the position information measured by the laser tracker 3, obtain the positions of the fixed section end face 1, the moving section end face 2 and the parallel mechanism 5 of the cabin section, and according to the obtained position information, Obtain the relative position data of the end surface 1 of the fixed section and the end surface 2 of the moving section through calculation, and control the parallel mechanism 5 according to the relative position data;
[0077] The laser tracker 3 is used to measure the position information of the end face 1 of the fixed se...
specific Embodiment approach 2
[0082] Specific embodiment 2: This embodiment is a further limitation of the automatic assembly system of the spacecraft cabin described in specific embodiment 1 on the ground. The master control system 4, according to the obtained position information, controls the parallel mechanism 5 to include :
[0083] According to the obtained position information, establish the calibration coordinate system O of the end face 1 of the fixed section 1 -X 1 Y 1 Z 1 and the calibration coordinate system O of the end face 2 of the moving section 2 -X 2 Y 2 Z 2 ;
[0084] According to the obtained position information, establish the parallel mechanism 5 coordinate system O when the parallel mechanism 5 rotates in three dimensions 3 -X 3 Y 3 Z 3 ;
[0085] When the distance between the end face 1 of the fixed segment and the origin of the coordinate system of the end face 2 of the moving segment is greater than or equal to (l+dl)mm, the calibration coordinate system of the end fac...
specific Embodiment approach 3
[0092] Specific implementation mode three: combination image 3 This embodiment is described. This embodiment is a further limitation of the automatic assembly system of the spacecraft cabin section on the ground described in the second specific embodiment. The laser tracker 3 is used to measure the end face 1 and The position information of the end face 2 of the moving section includes:
[0093] After measuring the target ball, output the three-degree-of-freedom coordinates of the center of the target ball;
[0094] Both the end face 1 of the fixed section and the end face 2 of the moving section are planes, and three reference points are respectively selected on the end face 1 of the fixed section and the end face 2 of the moving section, and a target ball is respectively fixed on the selected reference points;
[0095] The master control system 4 establishes the calibration coordinate system O of the end face 1 of the fixed section according to the obtained position inform...
PUM
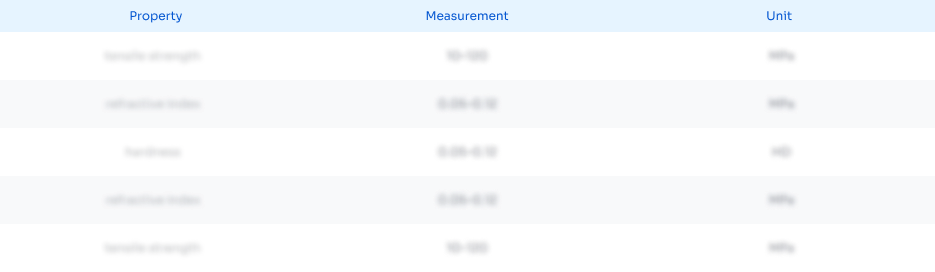
Abstract
Description
Claims
Application Information

- R&D
- Intellectual Property
- Life Sciences
- Materials
- Tech Scout
- Unparalleled Data Quality
- Higher Quality Content
- 60% Fewer Hallucinations
Browse by: Latest US Patents, China's latest patents, Technical Efficacy Thesaurus, Application Domain, Technology Topic, Popular Technical Reports.
© 2025 PatSnap. All rights reserved.Legal|Privacy policy|Modern Slavery Act Transparency Statement|Sitemap|About US| Contact US: help@patsnap.com