Method for breaking ice based on reducing supporting force of ice layer, and ice breaking ship
A support force and icebreaker technology, applied to icebreakers and other directions, can solve the problems of high tonnage requirements and high energy consumption of icebreakers, and achieve the effect of improving icebreaking efficiency
- Summary
- Abstract
- Description
- Claims
- Application Information
AI Technical Summary
Problems solved by technology
Method used
Image
Examples
Embodiment 1
[0020] like figure 1 As shown, the vortex-manufacturing icebreaker of the present invention includes an icebreaker 1 and a rotator 8. The rotator 8 is fixedly installed on the front lower part of the hull of the icebreaker 1 and is connected with the rotary drive system in the ship. The rotating part of the rotator is a bottom double A spoon-shaped tuning fork. When it is necessary to start the rotator to break the ice, the rotation of the rotator will create a vortex under the ice layer in front of the bow. The huge downward attraction of the vortex will reduce the local support force of the ice layer a lot, and the huge weight of the ice layer in this part will appear. Collapse tends to fracture the ice even under enormous downward stress.
Embodiment 2
[0022] like figure 2 Shown is the tubular type diversion device type icebreaker of the present invention, the fence nozzle 5 of tubular diversion device 2 is the water inlet when working, and its diameter is 2 meters, is designed with a gap, and the depth of the gap is 1.2 meters, mainly to prevent diversion. The negative pressure generated during the flow process and the buoyancy of the floating ring 7 cause the water inlet to stick to the ice layer and hinder the flow diversion. The function of the floating ring 7 is to keep the water inlet and the ice layer at an appropriate distance to ensure the best negative pressure. The design of the telescopic tube part 6 is mainly to be able to move properly when the ice layer breaks, so as to prevent the tube type flow guiding device 2 from being damaged. When the pump 4 in the fixed pipe part 3 is started, the water under the ice layer will quickly enter the pipe-type deflector 2 and flow out to the stern through the pipe. Water ...
PUM
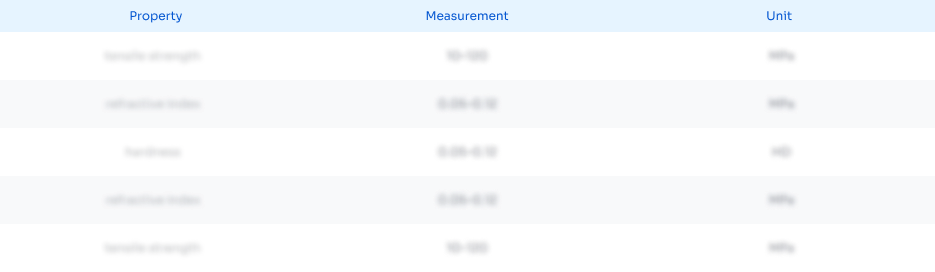
Abstract
Description
Claims
Application Information

- R&D
- Intellectual Property
- Life Sciences
- Materials
- Tech Scout
- Unparalleled Data Quality
- Higher Quality Content
- 60% Fewer Hallucinations
Browse by: Latest US Patents, China's latest patents, Technical Efficacy Thesaurus, Application Domain, Technology Topic, Popular Technical Reports.
© 2025 PatSnap. All rights reserved.Legal|Privacy policy|Modern Slavery Act Transparency Statement|Sitemap|About US| Contact US: help@patsnap.com