Dynamic liquid level wireless monitoring method and system
A wireless monitoring and dynamic technology, applied in the direction of engine lubrication, engine components, liquid level indicator, etc., can solve the problem that the dynamic tilt of liquid level cannot be applied, the sensor network system cannot be self-organized, and the monitoring interface lacks a graphical monitoring interface. And other issues
- Summary
- Abstract
- Description
- Claims
- Application Information
AI Technical Summary
Problems solved by technology
Method used
Image
Examples
Embodiment 1
[0106] The entire dynamic liquid level monitoring system of this embodiment mainly includes a data acquisition unit, a control unit, a wireless communication unit, a display unit, a voice broadcast unit and a terminal control unit.
[0107] Among them, the data acquisition unit adopts a plurality of HC-SR04 ultrasonic ranging sensors (this embodiment adopts 3 ultrasonic ranging sensors, and one of the ultrasonic ranging sensors is placed in the middle of the top of the container), which can be used when the liquid tilts left or right or Accurately measure liquid level height while tilting back and forth. The detection range of HC-SR04 ultrasonic ranging sensor is 2-400cm, and the accuracy can reach 0.3cm.
[0108] The wireless communication unit adopts Xbee-S2 module, which is compatible with Zigbee technology and can be set to point-to-point or transparent communication. The front-end display unit is a 2.8-inch ALIENTEK TFT-LCD module from ALIENTEK Company, which is used to ...
no. 2 example
[0113] The present invention can realize liquid level dynamic measurement, when the liquid tilting situation is such as Figure 6 In the case of left tilt as shown (at this time, the three sensors are located on the same horizontal straight line), the real height of the liquid level can be accurately known through the coordination and cooperation of multiple ultrasonic sensors. Ultrasonic sensor 2 is located in the middle of the top of the container.
[0114] From Figure 6 The calculation formulas of AB and BC can be obtained, in order to simplify the calculation, the present embodiment makes h 3 =h,x 1 =x 2 . The specific calculation formulas of AB and BC are as follows:
[0115] AB=AH+BH=(x×tanα) / 2+h-h 2 ,
[0116] BC=BG+GC=x / 2+cotα×(h-h 2 ).
[0117] Assuming that when the tilted liquid is placed in a horizontal state, the height from the bottom is H, and the width of the container is c, then there will be:
[0118] H×x×c=BC×c×AB / 2
[0119] Therefore:
[0120] ...
no. 3 example
[0125] The present invention can realize the dynamic measurement of the liquid level, when the liquid inclination is such as Figure 8 In the case of the forward tilt shown, the real height of the liquid level can be accurately known through the coordinated cooperation of multiple ultrasonic sensors. Ultrasonic sensor 2 is located in the middle of the top of the container.
[0126] From Figure 7 and 8 The calculation formulas of AB and BC can be obtained, in order to simplify the calculation, the present embodiment makes h 3 = h 1 , x 1 =x 2 =x 3 , x 3 is the vertical distance between two adjacent ultrasonic sensors, such as Figure 8 shown. The calculation process of analogy embodiment two has:
[0127] AB=(y×tanα) / 2+h-h 2 ,
[0128] BC=y / 2+cotα×(h-h 2 ).
[0129] Assuming that when the tilted liquid is placed in a horizontal state, the height from the bottom is H, the length of the container is x, and the width of the container is y, then there will be:
[01...
PUM
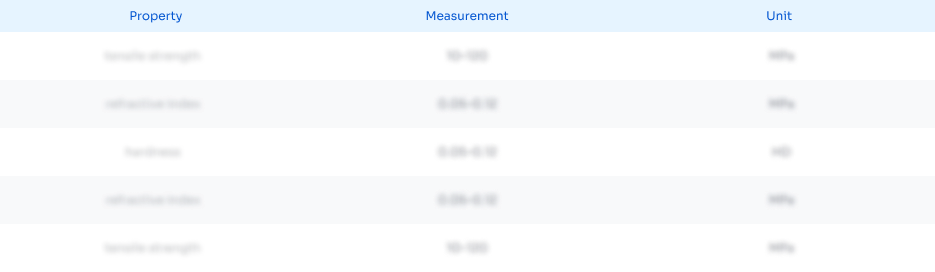
Abstract
Description
Claims
Application Information

- Generate Ideas
- Intellectual Property
- Life Sciences
- Materials
- Tech Scout
- Unparalleled Data Quality
- Higher Quality Content
- 60% Fewer Hallucinations
Browse by: Latest US Patents, China's latest patents, Technical Efficacy Thesaurus, Application Domain, Technology Topic, Popular Technical Reports.
© 2025 PatSnap. All rights reserved.Legal|Privacy policy|Modern Slavery Act Transparency Statement|Sitemap|About US| Contact US: help@patsnap.com