axial tensioner
A tensioner, axial technology, applied in spring/shock absorber, spring/shock absorber design features, spring, etc., can solve problems such as not very ideal, high manufacturing and use costs, complex structure, etc., to achieve load The effect of stable operation, low cost and convenient use
- Summary
- Abstract
- Description
- Claims
- Application Information
AI Technical Summary
Problems solved by technology
Method used
Image
Examples
Embodiment 1
[0028] axial tensioner, see Figure 3 to Figure 9 and the background technology, it is characterized in that it consists of a fixed sleeve 1, a gear sleeve 2, a pin shaft 3 and at least two centrifugal pendulums 4; The gear sleeve hole 1-1 is provided with at least two swing grooves 1-2 on the peripheral wall of the fixed sleeve, and a pin hole 1-3 is provided at the radial position of one end of each swing groove; the outer surface of the gear sleeve There are at least two tooth row grooves 2-1 on the top; the centrifugal pendulum is in the shape of a long strip, one end is provided with a pin hole 4-1, and an engaging tooth row 4-2 is provided on the edge position; the tooth sleeve is inserted into the fixed sleeve Then put the centrifugal pendulum into the swing grooves of the fixed sleeve respectively, so that the meshing teeth of the centrifugal pendulum and the tooth row grooves on the gear sleeve mesh together, and finally insert the pin shaft into the pin hole of the f...
Embodiment 2
[0035] Application examples of axial tensioners, see Figure 10 The difference from Embodiment 1 is that the centrifugal pendulum of this embodiment is provided with a guide chamfer 4-3. When this embodiment is in working state, when the centrifugal pendulum is opened due to rotation, the air driven by the guide chamfer is blown to the motor and other equipment to assist the equipment to dissipate heat.
Embodiment 3
[0037] Application examples of axial tensioners, see Figure 11 , embodiment two and embodiment one. The difference from Embodiment 1 is that the centrifugal pendulum of this embodiment is provided with a guide curved surface 4-4. Its function is the same as that of the guide chamfer in embodiment 2, that is, when the centrifugal pendulum is opened due to rotation, the air driven by the guide curved surface is blown to equipment such as motors to assist these equipment to dissipate heat. However, the air volume driven by the guide curved surface is larger, but the manufacturing cost is higher than that of the guide chamfer.
PUM
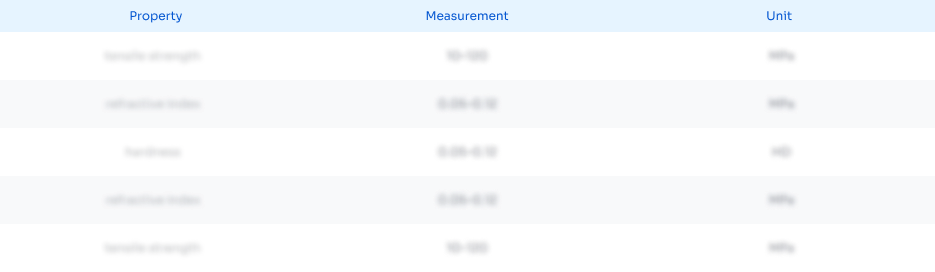
Abstract
Description
Claims
Application Information

- R&D
- Intellectual Property
- Life Sciences
- Materials
- Tech Scout
- Unparalleled Data Quality
- Higher Quality Content
- 60% Fewer Hallucinations
Browse by: Latest US Patents, China's latest patents, Technical Efficacy Thesaurus, Application Domain, Technology Topic, Popular Technical Reports.
© 2025 PatSnap. All rights reserved.Legal|Privacy policy|Modern Slavery Act Transparency Statement|Sitemap|About US| Contact US: help@patsnap.com