An anti-splash and anti-adhesion type process cavity for a track machine uniforming unit
A process chamber and anti-adhesion technology, which is applied in the field of process chambers, can solve problems such as backsplash and photoresist adhesion, and achieve the effects of reducing adhesion, improving performance, and increasing production capacity
- Summary
- Abstract
- Description
- Claims
- Application Information
AI Technical Summary
Problems solved by technology
Method used
Image
Examples
Embodiment Construction
[0019] The present invention will be further described below in conjunction with the accompanying drawings.
[0020] Such as Figure 1-3 As shown, the present invention includes an upper process chamber 2, a middle process chamber 3 and a lower process chamber 4, and the upper process chamber 2 and the middle process chamber 3 cooperate with the lower process chamber 4 respectively to form a whole. The upper process chamber inner surface 10 of the upper process chamber 2 is provided with an anti-splash groove 5 and coated with a hydrophilic layer.
[0021] Such as Figure 4 As shown, the anti-backlash tank 5 includes an upper back-splash tank and a lower back-splash tank, and the upper back-splash tank and the lower back-splash tank are along the upper process chamber inner surface 10 The grooves are concave upwards from top to bottom, and the wafer 1 is located between the lower edge 6 of the upper anti-splash groove and the lower edge 8 of the lower anti-splash groove. Th...
PUM
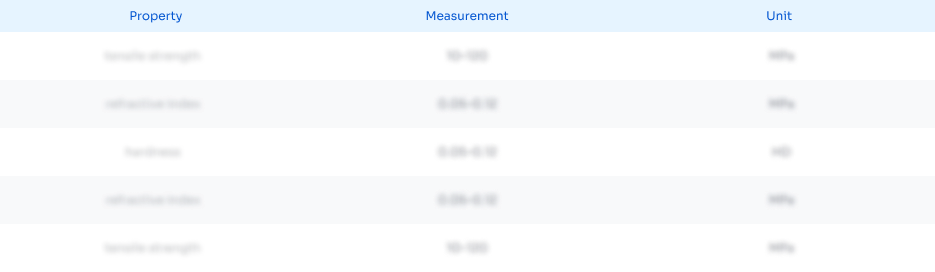
Abstract
Description
Claims
Application Information

- Generate Ideas
- Intellectual Property
- Life Sciences
- Materials
- Tech Scout
- Unparalleled Data Quality
- Higher Quality Content
- 60% Fewer Hallucinations
Browse by: Latest US Patents, China's latest patents, Technical Efficacy Thesaurus, Application Domain, Technology Topic, Popular Technical Reports.
© 2025 PatSnap. All rights reserved.Legal|Privacy policy|Modern Slavery Act Transparency Statement|Sitemap|About US| Contact US: help@patsnap.com