A temperature decoupling master-slave control method for multiple heating zones
A control method and heating zone technology, applied in heat treatment process control, manufacturing tools, heat treatment equipment, etc., can solve problems such as poor temperature uniformity, weak anti-disturbance ability, and inconvenient operation, and achieve low cost, convenient operation, and simplified strength Effect
- Summary
- Abstract
- Description
- Claims
- Application Information
AI Technical Summary
Problems solved by technology
Method used
Image
Examples
Embodiment 1
[0028] A multi-heating zone temperature decoupling master-slave control method is characterized in that it comprises the following steps:
[0029] The first step is to measure m different temperature points (ie, SV S0 、SV S1 ,...,SV Sm-1 ) temperature uniformity, and make the uniformity curve of each temperature measurement point, record the actual temperature of the steady state of n heating zones under the corresponding temperature measurement point (ie PV 0S0 、PV 0S1 ,...,PV 0Sm-1 ; PV 1S0 、PV 1S1 ,...,PV 1Sm-1 ;…;PV n-1S0 、PV n-1S1 ,...,PV n-1Sm-1 ;);
[0030] The second step is to determine m different temperature measurement points as typical temperature coupling points in each temperature zone, and set n 2×m dimensional decoupling arrays (VC) based on the temperature uniformity of the coupling points, each of which is decoupled The m elements in the first column of the array are the temperatures of the m temperature measurement points (ie SV S0 、SV S1 ,...,...
Embodiment 2
[0034] The present invention will be further described below in conjunction with the accompanying drawings and the examples. This example mainly uses a 3-temperature zone system (ie n=3) and 8 temperature uniformity detection points (ie m=8) to illustrate, and uses the 0th heating The zone is the main temperature control zone, the first heating zone is the slave control zone, and the second heating zone is the slave control zone, but this does not limit the present invention to the scope of the described embodiments.
[0035] see image 3 , Figure 4 , Figure 5 and Image 6
[0036] exist Figure 5 Middle SV—set temperature, PVB—decoupling output value, SV1—set temperature after decoupling, VC—decoupling vector, decoupling vector (VC) is a 2×8-dimensional real array, stored in the first column The temperature of 8 temperature measuring points, the second column stores 8 steady-state temperatures corresponding to the temperature measuring points, so that the temperature c...
PUM
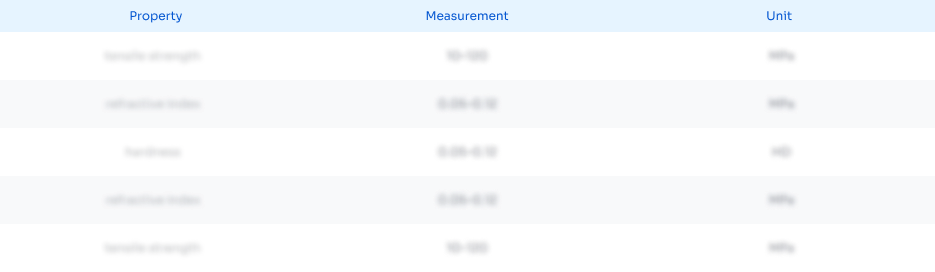
Abstract
Description
Claims
Application Information

- Generate Ideas
- Intellectual Property
- Life Sciences
- Materials
- Tech Scout
- Unparalleled Data Quality
- Higher Quality Content
- 60% Fewer Hallucinations
Browse by: Latest US Patents, China's latest patents, Technical Efficacy Thesaurus, Application Domain, Technology Topic, Popular Technical Reports.
© 2025 PatSnap. All rights reserved.Legal|Privacy policy|Modern Slavery Act Transparency Statement|Sitemap|About US| Contact US: help@patsnap.com