A closed-loop micro-displacement stepping drive device with variable step distance with displacement sensing function
A technology of stepping drive and displacement sensor, applied in measuring devices, piezoelectric effect/electrostrictive or magnetostrictive motors, generators/motors, etc., can solve the problem of low positioning accuracy and repeat positioning accuracy, and large structural size , Large travel displacement sensor is expensive and other issues
- Summary
- Abstract
- Description
- Claims
- Application Information
AI Technical Summary
Problems solved by technology
Method used
Image
Examples
Embodiment Construction
[0013] The detailed content and specific implementation of the present invention will be further described in conjunction with the accompanying drawings.
[0014] When using two sets of stepping piezoelectric actuator units as displacement actuators:
[0015] In the initial state, the hoop piezoelectric stack (2) (9) (17) (11) is powered on, the upper mechanism (3) and the lower mechanism (15) are fixed on the guide rail (1), and then the displacement sensor is recorded (6) and set it as the origin. When the movement starts, first turn off the hoop piezoelectric stack (9), release the locking mechanism (10) and the guide rail (1), and then apply a certain voltage to the stroke piezoelectric stack (4) to generate displacement. This makes the value of the displacement sensor (6) fixed on the upper mechanism (3) change, and this value is the stepping distance of the driver, which can be determined according to the voltage adjustment. Then power on the hoop piezoelectric stack (...
PUM
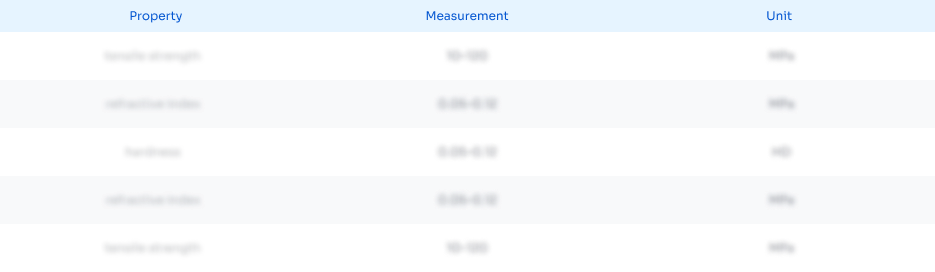
Abstract
Description
Claims
Application Information

- R&D Engineer
- R&D Manager
- IP Professional
- Industry Leading Data Capabilities
- Powerful AI technology
- Patent DNA Extraction
Browse by: Latest US Patents, China's latest patents, Technical Efficacy Thesaurus, Application Domain, Technology Topic, Popular Technical Reports.
© 2024 PatSnap. All rights reserved.Legal|Privacy policy|Modern Slavery Act Transparency Statement|Sitemap|About US| Contact US: help@patsnap.com