A kind of method of directly synthesizing cyclohexanol by cyclohexylamine
A technology of cyclohexylamine and cyclohexanol, applied in the field of chemical technology, can solve the problems of high production cost, low efficiency of cyclohexene, complicated process route, etc., and achieves simple synthesis method, simple and clean reaction conditions, and reaction yield. high effect
- Summary
- Abstract
- Description
- Claims
- Application Information
AI Technical Summary
Problems solved by technology
Method used
Image
Examples
Embodiment 1
[0025] In the autoclave, 1.6g of cyclohexylamine, 0.41g of 2% (wt) Ru / MCM-41 (molecular sieve) catalyst, 170ml of water and 10ml of tert-butanol (the molar ratio of which is 1:0.005:583:6.5) were successively added into the autoclave. Pass N 2 Make a replacement. Then the temperature was raised to 180°C, and the pressure of 3.0 MPa of hydrogen gas was introduced and maintained. After 8 hours of reaction, the hydrogen gas flow was stopped, and the temperature was lowered to room temperature. The catalyst and the reaction solution were separated by filtration under reduced pressure, and the reaction solution was extracted and separated by toluene to obtain an organic phase, which was analyzed by gas chromatography. The yield of the product cyclohexanol by quantitative calculation is 97.8%.
Embodiment 2
[0027] 1.6 g of cyclohexylamine, 0.41 g of 2% Ru / AC catalyst, 170 ml of water and 10 ml of tert-butanol (the molar ratio of which is 1:0.005:583:6.5) were successively added into the autoclave. Pass N 2 Make a replacement. Then the temperature was raised to 180° C., and the pressure of hydrogen was 2.0 MPa and maintained. After 8 hours of reaction, the hydrogen flow was stopped and the temperature was lowered to room temperature. The catalyst and the reaction solution were separated by filtration under reduced pressure, and the reaction solution was extracted and separated by toluene to obtain an organic phase, which was analyzed by gas chromatography. The yield of the product cyclohexanol by quantitative calculation is 99.5%.
Embodiment 3
[0029] Add cyclohexylamine 1.6g, 2%Ru / SiO 2 Catalyst 0.41g, water 170ml and tert-butanol 10ml (the molar ratio is 1:0.005:583:6.5). Pass N 2 Make a replacement. Then the temperature was raised to 180°C, and the pressure of 3.0 MPa of hydrogen gas was introduced and maintained. After 8 hours of reaction, the hydrogen gas flow was stopped, and the temperature was lowered to room temperature. The catalyst and the reaction solution were separated by filtration under reduced pressure, and the reaction solution was extracted and separated by toluene to obtain an organic phase, which was analyzed by gas chromatography. The yield of product cyclohexanol was 98.9% according to quantitative calculation.
PUM
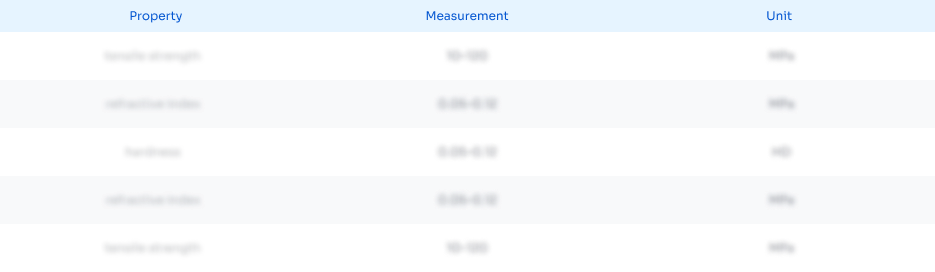
Abstract
Description
Claims
Application Information

- R&D
- Intellectual Property
- Life Sciences
- Materials
- Tech Scout
- Unparalleled Data Quality
- Higher Quality Content
- 60% Fewer Hallucinations
Browse by: Latest US Patents, China's latest patents, Technical Efficacy Thesaurus, Application Domain, Technology Topic, Popular Technical Reports.
© 2025 PatSnap. All rights reserved.Legal|Privacy policy|Modern Slavery Act Transparency Statement|Sitemap|About US| Contact US: help@patsnap.com